原料润磨后造球和焙烧过程研究与探讨
浏览:次|评论:0条 [收藏] [评论]
刘宝志 方 觉 魏 军 李 超 安志伟 王 东
刘宝志 方 觉 魏 军 李 超 安志伟 王 东
【摘 要】通过生产试验,研究了原料润磨比例对生球强度的影响,在实验室进行了不同温度的焙烧试验,得到原料润磨比例不同的球团矿并测得其常温抗压强度,使用一台可调气氛高温抗压试验机研究了球团矿氧化焙烧过程中热态强度的变化规律,通过试验结果分析了原料润磨对球团矿常温抗压强度和焙烧过程热强度的影响。
【关键词】润磨 造球 抗压强度 热强度
1.前言
由于球团工艺的特殊性,其对原料的性质要求较高,尤其对原料的粒度要求非常高。但是,目前国内适合造球的原料较少,我国自产的精矿不仅品位低,SiO2含量高,同时粒度偏粗,造成球团生产配加膨润土用量过大。近年来,为了提高球团矿产量和质量指标,降低膨润土用量,润磨技术在国内球团厂得到广泛应用。因此,有必要进一步了解润磨对造球的影响,以及润磨对球团矿抗压强度和氧化焙烧过程热强度的影响。
2.试验过程
我们分两部分进行试验,一部分在承德建龙
2.1 试验设备
主体设备为
实验室的主体试验设备是一台可调气氛高温抗压试验机和一台井式炉。使用可调气氛高温抗压试验机检测球团矿在焙烧过程中温度及相对应的热强度。使用一个井式炉,主要对不同试样在不同温度下进行焙烧,然后检测其抗压强度。
2.2 试验方法和过程
本次试验原料有两种精矿粉,分别为磁铁矿精矿粉和低钒钛磁铁矿精矿粉,除尘灰为竖炉电除尘收集的粉尘,化学成分见表1;膨润土成分见表2。
表1 铁精粉成分和配比
品种 |
TFe |
SiO2 |
水分 |
配比 |
备注 |
铁粉1 |
64.99 |
3.78 |
9.01 |
50% |
|
铁粉2 |
65.54 |
4.57 |
9.71 |
45% |
|
除尘灰 |
62.92 |
4.42 |
0 |
5% |
|
表2 膨润土指标
|
吸兰量 % |
蒙脱石 ml/ |
胶质价 g/ |
膨胀容 ml/mg |
水分 % |
细度 -325目 |
膨润土 |
25.35 |
57.36 |
960 |
31 |
13.32 |
90 |
承德建龙球团生产系统中,混合料烘干后,一部分原料经过润磨后进入造球机,另一部分不经润磨直接进入造球机,通过调整分料器控制润磨原料的比例。这次试验共分7组,混合料经过润磨的比例分别为:0,50%,60%,70%,80%,90%,100%。膨润土配比1.2%,混合料烘干后水分:6.0%。每组试验均进行24小时的试验,测定数据:生球落下强度,生球抗压强度。所得数据见表3。
表3 不同润磨比例生球的强度
试验组号 |
润磨比例/% |
落下强度/次 |
抗压强度/N |
膨润土配比 |
1 |
0 |
3.0 |
13.5 |
1.2% |
2 |
50% |
4.4 |
15.5 |
1.2% |
3 |
60% |
4.5 |
15.8 |
1.2% |
4 |
70% |
5.0 |
17.3 |
1.2% |
5 |
80% |
5.5 |
20.0 |
1.2% |
6 |
90% |
5.0 |
18.5 |
1.2% |
7 |
100% |
4.8 |
18.0 |
1.2% |
在生产试验中,选取现场试验中不同混合料经过润磨的比例情况下的7组生球试样。试样选取粒度范围为10~12mm的生球。将选取的试样放在烘干箱内,
本试验将准备好的球团试样分别放在井式炉进行生球氧化焙烧。
待焙烧过的球团矿完全冷却后,在每组试样中挑选形状规则、粒度为10~12mm球团矿60个,利用弹簧压力机测定其抗压强度,取其平均值作为该种球团矿的常温抗压强度。所得数据见表4。
表4 氧化焙烧过程中球团矿单球抗压强度/ N
润磨比例/% |
|
|
|
|
|
|
|
|
0 |
192 |
273 |
344 |
508 |
854 |
1017 |
636 |
76 |
50 |
210 |
379 |
407 |
759 |
681 |
865 |
571 |
61 |
80 |
253 |
320 |
644 |
809 |
1035 |
1163 |
604 |
130 |
100 |
184 |
350 |
416 |
679 |
801 |
1020 |
602 |
75 |
平均 |
210 |
331 |
453 |
689 |
843 |
1016 |
603 |
86 |
本实验测定球团矿焙烧过程中抗压强度。本实验检测4组试样的焙烧过程的抗压强度,原料润磨比例分别为0、50%、80%、100%,检测温度分别为常温、
挑选直径为11±
表5 不同焙烧温度的球团矿抗压强度/ N
润磨比例/% |
|
|
|
|
0 |
817 |
1244.4 |
2391.7 |
3127.6 |
50 |
1000 |
1567.5 |
2342.5 |
2911.9 |
80 |
931.6 |
1723.7 |
2920 |
3425 |
100 |
897.4 |
1439.5 |
2827.5 |
3765 |
3.试验结果分析
3.1 润磨比例对生球强度的影响分析
根据表3所得结果,润磨比例与生球抗压强度和落下强度的关系如图1所示:
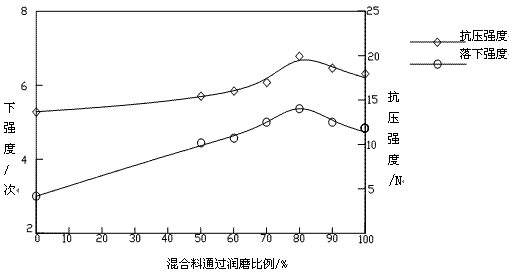
图1 生球强度与润磨比例的关系
根据图1所示可以很明显地看出:在承德建龙原料和工况条件下,润磨比例在80%左右生球抗压强度和落下强度最好。润磨比例低于80%时,随着润磨比例的增加,生球的抗压强度和落下强度呈明显的上升趋势,超过80%以后生球的抗压强度和落下强度反而下降。但是,100%通过润磨时生球强度指标均大大好于不通过润磨,说明润磨能够明显改善物料的成球性能,大大改善生球的强度。
3.2 球团矿抗压强度与焙烧温度的关系分析
根据表4所列出的不同焙烧温度的球团矿常温抗压强度检测结果,做出不同润磨比例的球团矿常温抗压强度与焙烧温度的关系曲线,如图2所示。
图2 球团矿常温抗压强度与焙烧温度的关系图
从图2可以很明显地看出:球团矿的单球抗压强度随着焙烧温度的逐渐提高,呈相关上升的趋势,焙烧温度越高,单球抗压强度越高。
目前,一般中小高炉要求球团矿单球抗压强度不小于1000 N。为了满足这一要求,焙烧温度不能过低。也就是说,图中单球抗压强度与焙烧温度的关系决定了一个最低焙烧温度tmin。焙烧温度不低于这个值时才能保证球团矿单球抗压强度满足一般中小高炉的要求。
tmin的值较为明确,可由图2直接得到。在每一条曲线中与抗压强度等于1000 N对应的温度即为该配矿的最低焙烧温度。
3.3 球团矿氧化焙烧过程中热强度变化规律分析
根据表5所得结果,做出混合料不同润磨比例的球团矿在氧化焙烧过程中抗压强度与焙烧温度的关系曲线,如图3所示。
图3 氧化焙烧过程中球团矿抗压强度与温度的关系图
从图3当中明显的看出,在氧化焙烧的升温过程中,球团矿强度与温度的关系曲线呈现出一种不对称的两头低中间高的形态,即当焙烧温度升高到一定程度后球团矿的强度将开始降低。
在温度提高时,矿粉颗粒之间产生固相反应而提高强度,球团矿的抗压强度在低温段均随着温度的升高而提高。不过,球团矿在高温下会产生液相,颗粒之间的结合力也会降低。因此,强度达到一个最高值后,转而随温度的提高而下降。
高温球团矿在竖炉中处于料柱下部,要承受较大的挤压力。一旦抗压强度过低,极易大量破损。也就是说球团矿在氧化焙烧过程中的强度变化规律决定了一个最高焙烧温度tmax。焙烧温度不高于这个值时才能保证球团矿在焙烧过程中不产生大量破损。
对于竖炉而言,当球团矿的抗压强度下降至500 N时,竖炉内不会发生问题。图3每一条曲线与抗压强度等于500 N对应的温度中,较高的一个即为tmax。
3.4 球团矿tmin和tmax
通过以上分析,求得不同润磨比例的球团矿tmin和tmax如下:
表6 球团矿焙烧温度
润磨比例 |
tmin /℃ |
tmax /℃ |
0 |
1077 |
1110 |
50% |
1054 |
1111 |
80% |
1056 |
1126 |
100% |
1062 |
1114 |
平均 |
~1062 |
~1115 |
从表10所得结果可以看出,尽管润磨对球团矿tmin和tmax影响不大,但研究结果仍能反应一种趋势。不润磨时的tmin高于润磨时的tmin。这说明润磨对提高球团矿强度有利,在较低焙烧温度可以获得较高强度,或者说获得相同强度需要的焙烧温度较低。润磨比例80%时的tmax高于其他情况,而不润磨时tmax最小。说明润磨能够提高tmax,润磨有利于提高球团矿焙烧过程的热强度,减少氧化焙烧过程球团矿破损。
3.5 润磨对球团矿焙烧过程热强度和常温抗压强度影响
从图2中看出,球团矿抗压强度在温度较低(
从图3中看出,润磨比例80%的时候,球团矿氧化焙烧过程中热强度明显高于其他情况。这种现象与生球强度相对应,说明生球强度越高,在氧化焙烧过程中球团矿热强度越好。因此,造好生球,提高生球强度是提高球团矿强度,减少球团矿在氧化焙烧过程破损的一项重要措施。
在试验的原料条件下,在较高温度焙烧时,润磨比例越高,球团矿抗压强度越好。这是由于润磨比例提高,原料中细颗粒增多,比表面积增多,颗粒之间增加了接触面积,为焙烧过程中的固相扩散和再结晶创造了良好条件,有利于球团矿强度提高。
另据研究表明润磨技术可以改善球团原料的焙烧性能,降低预热温度和焙烧温度,缩短预热时间和焙烧时间,所以有利于提高球团矿抗压强度。
4.讨论
根据现场试验和实验室研究,得出以下结果:
4.1 润磨可以改善原料的成球性能,对造球产生很大影响,但并不是100%通过润磨最好,试验表明,承德建龙原料的润磨比例在80%左右综合效果最好。
4.2 球团矿在氧化焙烧过程中的强度变化规律就决定了一个最高焙烧温度tmax,焙烧温度不高于这个值时才能保证球团矿在焙烧过程中不产生大量破损。
4.3 为保证高炉冶炼的顺利进行,球团矿必须具有一定的强度。一般中小高炉要求球团矿单球抗压强度不小于1000 N。为了满足这一要求,焙烧温度不能过低。从图3可以看出,球团矿的单球抗压强度随焙烧温度的提高而上升。通过单球抗压强度与焙烧温度的关系可以确定一个最低焙烧温度tmin。为了保证球团单球抗压强度满足高炉冶炼需要,实际焙烧温度必须大于最低焙烧温度tmin。
4.4 原料润磨比例可以提高球团矿氧化焙烧过程中热强度,热强度提高的程度与润磨比例有关。
4.5 润磨可以提高球团矿的抗压强度。润磨比例提高,球团抗压强度基本上呈现上升趋势,而在焙烧温度较高时更加明显。
4.6 润磨可以降低球团矿tmin,提高球团矿tmax。在承德建龙的原料条件下,球团矿的焙烧温度大约为:tmin=
5.结束语
由于近年来润磨在球团生产中得到广泛应用,发挥着越来越重要的作用,关于润磨机理以及对造球方面影响的研究已经很多。本试验重点从原料润磨比例对生球强度的影响,以及从润磨球团焙烧过程和球团强度等影响几方面进行了探讨,未考虑原料性能、水分控制、设备参数和其他方面的影响,存在许多不足,今后,进一步深入研究和了解润磨作用仍是我们的任务。
参考文献
1.刘华. 润磨技术在济钢球团生产中的应用[J].烧结球团,2000,25(4):55~57。
2.解珍健,节永烈.润磨工艺在马钢球团生产中的应用[C],2006年全国烧结球团技术交流年会论文集,呼和浩特,全国烧结球团信息网,2006,196~199。
3.傅菊英,范晓慧等.涟钢混合料润磨对球团过程的影响[J].烧结球团,2001(5): 15~17。
4.龚瑞娟.球团矿焙烧与还原过程中的热强度研究[D] 唐山:河北理工大学大学硕士论文,2006。
5.范晓慧,傅菊英,朱德庆等.改善竖炉球团矿质量的研究[C],竖炉球团(铁矿球团论文选辑之三),呼和浩特:全国烧结球团信息网,2006,4~7。
摘自《2009全国烧结、球团、炼铁技术及生产年会》
延伸阅读
- 上一篇:马钢150万t球团链蓖机回转窑控制系统 下一篇:成品皮带自动布料改造的实践