采用CFX对高炉回旋区的模拟研究
浏览:次|评论:0条 [收藏] [评论]
摘要:考虑到回旋区内存在的焦炭热解、燃烧、气体湍流化学反应等过程,利用CFX,建立了基于颗粒轨道的物理模型,并对该模型进行了数值模拟。模拟结果表明:回旋区内,气流呈双涡旋分布,气体速度大部分<16m/s,峰值温度在2670K左右。进行了高炉红外测温实验,测量的峰值温度约为2660K。实验验证了数值模拟结果基本是正确的,对进一步研究高炉回旋区和修改高炉基本操作制度提供了理论依据。
关键词:高炉回旋区;数学模型;数值模拟
1 前言
高炉回旋区对高炉起非常主要的作用。笔者在文献中建立了回旋区冷态试验模型,采用激光PDA对回旋区内气、粒两相特性进行研究。但由于回旋区内物理化学过程的复杂性,目前回旋区理论仍缺乏完整的描述。全面研究回旋区的特性必须采用计算流体力学(CFD)的方法。
CFX是最成熟的商品化CFD软件之一,提供了被工程广泛验证的多种三维复杂湍流流动模型,化学动力学模型,多相流模型,气态、固态颗粒燃烧模型,辐射模型和颗粒输运模型等;拥有针对流体问题的最新网格生成技术;提供的基于改进的SIMPLE算法则包含多种求解模块的求解器,具有高可靠性和强大的计算能力;提供了领先的数据可视化后处理技术。
本研究考虑到回旋区内存在的颗粒运动、挥发、燃烧以及化学湍流现象,利用CFX建立了颗粒轨道的三维湍流数学模型,模拟回旋区内部的状况,分析其内部气体、颗粒的物理化学规律。为检验计算结果的正确性,进行了高炉红外线测温实验,通过大量高炉操作实践验证了数学模型是正确的,为高炉基本操作制度的修订提供了理论依据。
2 回旋区大小计算
大量高炉操作经验证明,高炉鼓风动能与高炉回旋区之间存在如下关系公式:
Eb=2ρgVg2TgP0/(3600πT0Pgd2n), (1)
ιR=0.118×10-3Eb 0.77, (2)
HR=ιR/KR, (3)
式中Eb为高炉鼓风动能;Vg为每分钟鼓风量;ρg为鼓风密度;Tg为鼓风温度;Pg为鼓风压力;T0为273K;P0为标准大气压;n为风口个数;d为风口直径;ιR为回旋区深度;HR为回旋区高度;KR为回旋区形状系数。
依据高炉风口的相关参数,即可估算出回旋区的大小。莱钢某在线运行的750m3高炉风口的参数值有:鼓风压力2.15kg/cm2,风口直径0.12m,风口数量为18,鼓风温度1050℃,进风量1800m3/min。将数据带入公式中,计算出该回旋区的深度约为1.11m。根据小高炉取小值的经验,并取回旋区形状系数为1,故算出该回旋区的高度约为1.11m,回旋区近似为直径1.11m球体。
3 回旋区物理模型
3.1 回旋区的几何模型
ANSYS ICEM CFD 5.1具有极强的几何建模能力和自适应网格划分等技术。应用该软件,依据计算的回旋区尺寸,建立其几何模型。利用软件的自适应网格划分技术,对几何模型进行相应的网格划分。采用的笛卡尔坐标系方向:x轴为回旋区进风管轴向,z轴为高炉的高度方向,y轴为垂直于xz平面的水平面。坐标原点为进风管进入高炉后的位置。
3.2 回旋区的CFX模型
将划分完网格之后的几何模型导入CFX5.7.1一pre中,设置边界条件:气流速度、温度和压力的值为高炉风口参数值;焦炭颗粒直径取10mm;焦炭颗粒估计温度为1900K;在此忽略硫分,取焦炭颗粒灰分12%,挥发分1.0%,焦87%;颗粒初始速度设为1m/s,方向为-z;假设壁面光滑、绝热,与颗粒之间为弹性碰撞。
受计算机计算能力影响,只分别在z=0、0.1、0.9m层加入颗粒。每层颗粒数为1000,在每一层的分布位置是随机的。
选择CFX 5.7.1提供的流体力学模型和颗粒燃烧、颗粒输运模型、传热模型,设定此次计算的收敛精度、迭代次数和次序等参数,引入CFX Solver5.7.1进行计算,可完成回旋区数学模型的建模、数值模拟计算。
4 数值模拟结果分析
改变风口入口参数,利用CFX可模拟不同工况下的回旋区的物理化学状态,分析颗粒、气体湍流特性、温度及浓度等空间分布。在此主要通过CFX后处理模块POST 5.7.1对数值模拟结果中的气体速度、温度以及CO、CO2、O2组分进行分析。
4.1 xy平面内气体速度分布
图1为气体在回旋区xy平面内(z=0)的速度矢量。气体从左侧中心进入(下同)。与焦炭颗粒相互作用下,近风口区气体速度梯度较大,整个回旋区绝大部分气体的速度<16m/s,在y=±0.3m的位置形成两个气流漩涡。
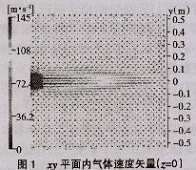
4.2 xy平面内气体温度分布
图2为回旋区在xy平面内的气体温度分布(z=0)。进入风口后,氧气与焦炭发生完全燃烧,释放热量。具有一定体积的焦炭与氧气的反应并非瞬间完成,受高速气体影响,焦炭与CO2不断向外围移动、扩散,在火焰外围达到较高的温度。周围气体温度低,是由于焦炭的熔损反应的缘故。在该平面内峰值温度为2670K,约为2400℃。
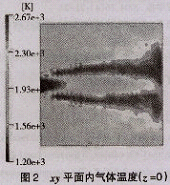
为检验数值模拟结果的准确性,对高炉回旋区进行了红外测温实验,红外玻璃可通过波长范围为0.8~1.2μm。图3为红外测温实验结果,测出的回旋区峰值温度为2390℃,约为2660K。比较图2和图3温度的结果,数值模拟温度基本与红外方式获得的温度相等。说明采用CFX的温度模拟结果基本反映回旋区的状况。
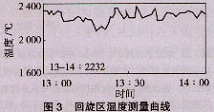
4.3 xy平面内气体CO组分分布
图4是CO在y平面的浓度分布(z=0),除中心地带浓度较低之外,其它区域浓度大于10%,峰值达到了27.4%。利用CFX可以得到任意z平面的CO浓度分布图。研究CO浓度对推断高炉软熔带的基本形状有比较重要的意义。
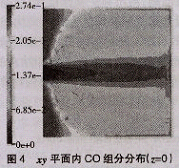
4.4 xy平面内气体CO2组分分布
图5是C02分别在z=0xy平面分布。受高速气流影响,CO2主要在燃烧火焰的外围空间分布。由于熔损反应,更外围空间,浓度降低。在z=0xy平面内平均浓度大于8.5%,峰值达到17%。
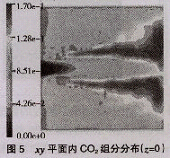
4.5 xy平面内气体O2组分分布
图6是02分别在z=0xy平面分布。在与焦炭的作用下,氧气的消耗很大,除在进风口外,其它各区的浓度下降到1%以下。
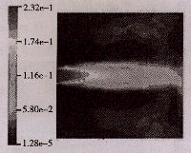
5 结论
考虑了回旋区内焦炭热解、燃烧以及与气体化学反应、颗粒轨道运动以及气流的湍流行为,利用CFX建立了回旋区三维湍流物理模型,并进行了数值模拟,得到了大量描述回旋区特性的数据。模拟结果显示:回旋区内气体成双涡旋分布,绝大部分气体速度<16m/s;回旋区峰值温度在2670K左右,基本与红外测量的结果相等;在颗粒粒子数目为1000的情况下,在z=0 xy平面内CO、C02气体的峰值浓度分别为27.4%和17%。
数值模拟结果基本与高炉实践结果吻合,较好地反映了回旋区内部的状态,为高炉操作制度提供了理论依据。
- [腾讯]
- 关键字:无