冷带钢轧制及连续退火技术研发与展望
浏览:次|评论:0条 [收藏] [评论]
目前,串列式冷轧轧制的全连续化和冷轧与酸洗的直接化已经成为冷轧工艺的基本模式。连续化生产的进一步发展是连续退火的直接化。2000年以后,以提高板厚控制精度和平坦度控制精度为主要目的的…
目前,串列式冷轧轧制的全连续化和冷轧与酸洗的直接化已经成为冷轧工艺的基本模式。连续化生产的进一步发展是连续退火的直接化。2000年以后,以提高板厚控制精度和平坦度控制精度为主要目的的小直径工作辊6辊UC轧机4机架串列式机组投入工业生产。该系统酸洗前配置除鳞轧机进行机械除鳞,提高了酸洗效率,冷轧机组采用液压压下和高应答AC马达驱动,对板厚和张力进行无干扰控制,提高了板厚精度。此外,在轧机入口和出口配置板形仪,在轧机之间配置平坦度计量仪,将带钢形状的实测值与设定值进行比较,对平坦度和边降进行控制,使高尺寸精度、高平坦度和高表面质量的高级冷轧板制造成为可能。
1、冷轧板厚度控制
影响冷轧板厚度偏差的因素有:热轧加热炉滑轨造成的黑印、在热轧输出辊道上冷却引起的变形抗力波动、冷轧中焊接点通过时减速加速引起摩擦系数变化导致的轧制负荷波动等。此外,轧机间张力的波动、支撑辊偏心、轧机刚性不足也对钢板厚度精度有影响。使用液压厚度自动控制技术(AGC)可以减小这些因素对钢板厚度的影响。
近10年来,对基于数学物理模型的先进板厚控制系统进行了大量研究。其中有利用最佳非线性控制的、对板厚和张力进行实时控制的仿真技术,仿真控制结果可使板厚和张力在总体上达到目标值,但带钢开始加速点的板厚和张力与目标值仍有偏差,这是一个需要解决的问题。此外还有利用基于广义最小二乘法的ARMAX模型,根据测定的轧制数据,对钢板厚度进行确认的方法,以及利用该方法对可逆式冷轧机进行厚度前馈控制的技术。
板厚控制仿真技术有了进一步发展并已在实际冷轧工艺中得到应用。利用该技术开发出适用于串列式冷轧机组的轧制规程设计方法。这种设计方法利用仿真技术得出高精度板厚和高生产率的评价函数并确定轧制作业中的限制条件,在此基础上对轧制规程进行设计。轧制规程优化设计的结果,由于减少了轧制线负荷,马达电流超过8000A的情况大大减少。进一步发展这种控制方法,开发出无须假设轧制变量的概率分布,利用已有的轧制输入、输出数据和轧制模型进行包括轧制变量波动因素在内的轧制规程进行设计。采用这种方法使高强度钢板厚度不合格率减少了13%-35%。
对板厚控制的轧机间最佳张力的问题和串列式冷轧机组的反映张力目标值-轧制速度关系的张力曲线的优化问题进行了研究。利用这种方法进行板厚控制的特点是,将优化控制问题作为仅利用静态轧制模型进行处理的问题,所以计算时间短,可以获得稳定的最佳值。具体方法是,将张力曲线的优化分2个阶段进行。在第1阶段设定板厚波动的目的函数和轧制负荷波动的目的函数的权重,分别求出摩擦系数等因素变化时的张力曲线。第2阶段,调整第1阶段设定的目的函数的权重,使各个张力曲线都满足规定的条件。实验表明采用这种厚度控制方法使减速轧制时钢板厚度不合格率降低37%。
串列式冷轧机组使用AGC对支撑辊进行偏心控制的厚度控制方法是在各个轧机上配置AGC,采用这种厚度控制方法的一个实例是,厚度为1.2mm的冷轧钢板正常部位的厚度精度由±0.7%提高到±0.5%。
近10年来,基于轧制理论的先进板厚控制技术、仿真技术有了很大发展。开发出通过提高AGC功能的控制增益设定、针对轧制实况设定轧制条件限定值的板厚高精度控制方法。此外,还对非正常部位(焊接点穿带时、加减速轧制时)的厚度控制问题进行了研究。
2、冷轧板边降控制
边降是轧材宽度方向边部厚度突然减薄的现象。边降控制一方面可以满足冷轧薄板用户对钢板的板厚精度和断面轮廓形状日益严格的要求,同时,可使冷轧厂减少钢板切边量,提高成材率。此外,小边降冷轧板有利于用户加工自动化和提高加工效率。有效控制边降的轧机是PC轧机、HC(UC)轧机、锥形工作辊移动轧机。
采用的阶梯形单辊移动边降控制系统由4机架串列式机组构成,控制系统由机组出口的边降检测器进行反馈控制、各轧机工作辊最佳移动量控制、操作侧和驱动侧的非对称移动量控制和边降平坦度非相干控制构成。
HC(UC)轧机的平坦度控制机构的中间辊移动装置、工作辊弯辊装置和中间辊弯辊装置也具有减少边降的功能。为了对串列式冷轧机组边降现象进行分析,建立了基于平面法的三元轧制解析模型,利用该模型对边降仿真控制和实际生产线的边降控制进行了研究。在研究的基础上开发出4机架6辊轧机串列式冷轧机组的边降控制系统,用于实机作业取得了减少边降的效果。
3、冷轧板宽度控制
冷轧过程中的宽度控制问题是对钢板宽度边缘金属塑性流动的控制问题。因此,宽度控制引起的钢板宽度边缘变形对钢板的平坦度、凸度和边降都有影响,在研究冷轧板宽度控制时,对此不能忽视。
串列式冷轧机组轧制速度变化时的宽度边缘金属塑性流动会引起宽度的变化,对该现象进行了研究,提出了通过利用控制平坦度的弯辊装置控制边降来控制板厚波动的方法。利用实验对轧制加减速时的速度变化对钢板断面轮廓变化的影响和钢板断面轮廓变化对钢板宽度波动的影响进行了研究。钢板宽度波动主要发生在轧制速度发生变化的时候,宽度变化量与轧制时宽度方向金属流动引起的钢板断面轮廓变化量成正比(见图1)。基于这种认识,提出了根据轧制速度变化,控制轧辊弯曲装置来抑制钢板宽度波动的方法,经实验证明效果良好。
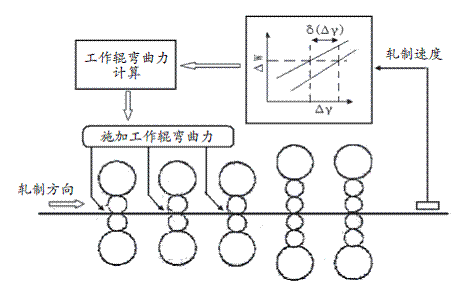
4、冷轧板平坦度控制
4.1、串列式冷轧机组平坦度控制
串列式冷轧机组冷轧钢板的平坦度对中间轧制的操作稳定性和其后续工序连续退火的通板性有很大影响,因此平坦度控制对提高生产效率和成材率是十分重要的。钢板平坦度不良的原因是,母板长度方向、宽度方向变形抗力不均匀引起轧制负荷波动,使轧制中工作辊弹性变形量发生变化以及工作辊局部热凸度增大。
在近10年冷轧板平坦度控制技术的发展中,采用了通过预测进行反馈控制的方法。由于这种方法实行了动态控制,减少了轧机入口钢板平坦度不良引起的轧制不稳定状态,使得在最后一架轧机可以对平坦度进行自适应控制。
对于串列式冷轧机来说,不仅厚度和张力控制对平坦度控制有效,而且对各轧机马达电流和电压进行适宜控制的轧机平衡控制系统(MBC)对平坦度控制也很有效。这种轧机平衡控制系统采用基于轧制理论的控制模型和多变数控制系统LIQ设计方法,在设定条件和实际操作情况发生偏离或马达电流过大时,可以在轧制速度不变的情况下降低电流,将轧制负荷的波动分散在各个轧机上,使钢板的不平坦度控制在0.6%,并保持较高生产率。
在单机架冷轧机平坦度控制方面,有一种方法是测定平坦度随时间的变化,建立时间滞后模型,利用该模型预测与冷却剂在钢板宽度方向上的喷射状态相对应的、一个控制周期后的平坦度变化量,根据该预测值,设定冷却剂喷射状态,对钢板平坦度进行控制。利用该项技术抑制了钢板端部平坦度的变化,获得了良好的平坦度。还有一种采用“平坦度影响系数”,利用平坦度控制系统进行平坦度控制的方法,该方法适用于4、6辊冷轧机的平坦度控制。这种方法将平坦度影响系数与轧辊变形和钢板变形联系起来,将钢板宽度方向分为若干区域,求出各个区域的平坦度影响系数,利用分区平坦度影响系数求出工作辊弯辊、中间辊弯辊(6辊轧机)、以及轧辊移动等装置的控制量,进行平坦度控制,并用局部冷却方法对控制残差进行补偿。
4.2、多辊轧机的平坦度控制
多辊轧机的平坦度控制方法有许多类型。例如有利用20辊森吉米尔轧机支撑辊程序控制模型进行平坦度控制的方法。还有在AS-U凸度调整中引入FSBA装置扩大平坦度控制能力的方法。森吉米尔轧机中间辊采用凹面形轧辊可减少轧材的局部延伸。
根据保证刚性的要求,20辊森吉米尔轧机采用了整体框架式牌坊,但最近开发出分体牌坊式20辊超级森吉米尔轧机(HZ轧机)。对轧机部件的形状尺寸进行最佳化设计,弥补了分体牌坊引起的刚性下降,保证了高刚性的要求。利用牌坊上下分体结构的特点,配置了高应答液压压下系统和控制平坦度的双AS-U机构,扩大了板厚精度和平坦度的控制能力,在此基础上对基于模糊神经网络模型的平坦度控制系统进行最佳化处理,提高了冷轧钢板的质量。
冷轧系统中检测高张力下钢板平坦度的功能对于平坦度控制十分重要。平坦度检测装置由分体型发展到第3代整体型检测辊,并开发出平坦度控制系统,对于轧制极薄硬质带材的多辊轧机提高生产效率和产品质量起了很大作用。
5、冷轧润滑和平整轧制技术
近10年来,冷轧技术研究的一个特点是对轧制引起钢板表面结构变化进行了大量的研究,其中有很多是关于平整轧制中钢板表面结构形成机制的研究。当用平均粗糙度对平整轧制后的镀锌钢板表面粗糙度进行评价时,轧机工作辊表面粗糙度的复制率约为60%,工作辊直径越大,工作辊粗糙度越容易复制到钢板上。
用平整轧制液对低碳钢板进行平整轧制,利用摆式试验测定平整轧制液的摩擦系数,考察摩擦系数对粗糙度复制率的影响。实验结果表明,当平整压下率小于4%时,使用摩擦系数小的水系平整轧制液进行平整,钢板表面粗糙度复制率高于干式平整轧制。此外还考察了平整轧制张力和轧制速度对粗糙度复制率的影响。张力大时,使用平整轧制液进行平整的粗糙度复制率高于干式平整;张力小时,两者的差别很小,但在最小张力的情况下,干式平整的粗糙度复制率反而高于轧制液平整。高速平整的粗糙度复制率高于低速平整。
对平整轧制中的钢板材质、工作辊钝化加工方法和工作辊直径等因素对粗糙度复制行为的影响进行了实验研究,对于SPCC-AB钢板,工作辊直径不同,粗糙度复制率不同,但对于S65C钢板复制率没有差别,软材质的SPCC-AB钢板的粗糙度复制性良好。
在平整轧制解析方法方面,开发出基于有限元法的图像电子放大平整轧制解析模型,对粗糙度复制时的材料行为和粗糙面形成机制进行了宏观和微观研究。通过微观解析计算,得出了钢板在粗糙度复制时的表面应变分布情况,阐明了粗糙面形成机制。此外,将平整轧制看作是平板压缩过程,利用弹塑性FEM解析模型,将平整轧制钢板咬入区分为粘着区和滑动区,阐明了钢板的变形机制。
关于平整轧制中钢板表面性状形成机制的研究和提高高强钢板平整轧制表面性状技术的研究将是今后平整轧制技术的研究方向。
6、高强度钢板冷轧技术
汽车采用高强度薄钢板,可实现车体轻量化。因此对高强度冷轧钢板新材料的开发研究做了大量工作。目前,关于高强度钢板的冷轧技术仍处于研究状态。
6.1、高强度钢板冷轧技术研究课题
高强度钢冷轧技术最大的研究课题就是高轧制负荷问题,并且高强度钢板一般要轧成比传统钢板更薄的厚度。因此,高强度钢冷轧需要解决以下问题。①因轧机能力所限,生产效率下降和宽幅钢板生产受限的问题;②轧制作业稳定性问题;③高负荷轧制中的平坦度控制问题;④高负荷轧制中的断面尺寸控制问题(板厚精度、边降);⑤连续轧制中的厚度变更和焊接性问题(和普通材的焊接);⑥高强度钢冷轧轧辊和轧制油问题(小直径轧辊、抗剥落性;最佳摩擦系数、打滑、粘结)。
高强度钢板的冷轧变形抗力取决于根据材料性能要求设计的钢成分和制造条件。因此,冷轧变形抗力达到什么程度是不能一言以蔽之的。
6.2、高强度钢冷轧技术的开发
实验表明,钢的强度越高,大压下时的摩擦系数越小。因此,需要开发既可大压下又不打滑的高强钢轧制润滑油。为使轧制中不发生轧辊和轧材的热黏结和轧辊表面的剥离,轧制油应具有高皂化值和低黏度。与传统轧制油相比,使用开发油轧制时前滑率增加,在高轧制速度区域也可以实现稳定的轧制作业。与普通钢相比,440MPa级高强钢轧制时容易发生打滑,所以应使用摩擦系数较大的、抗热黏结性良好的轧制油。这种轧制油不仅适用于高强钢的轧制,而且对于串列式冷轧机对镀锡板用原板进行高张力轧制也有很好的作用。
高强钢轧制对冷轧机提出的研究课题和应用技术开发如图2所示。
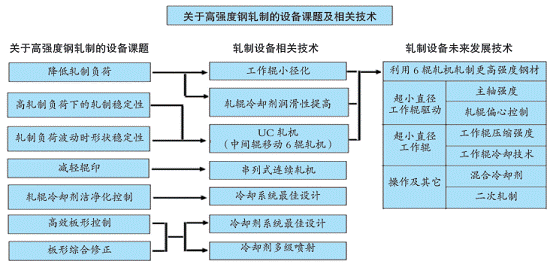
7、连续退火技术
与过去的罩式炉退火相比,连续退火具有生产效率高、处理时间短、处理质量均匀等优点,除了特殊用途钢板,连续退火已经是冷轧钢板主要的热处理方式。连续退火生产线将电解脱脂、退火(加热带、冷却带)、平整轧制、检测、精整等生产环节统合在一条生产线上,并利用自动化检测装置对材料内部缺陷和表面缺陷进行检测,使产品质量得到保证。此外,还利用退火速度自动控制系统使退火作业高速稳定进行。
对退火炉加热带采用蓄热式辐射管烧嘴(HRS-RT)进行加热的技术进行了研究。采用蜂窝式陶瓷蓄热体提高了热回收效率,在炉温不变的情况下,空气预热温度从原来的600K,提高到1100K,节约能源30%,NOX浓度约降低10%。
在直焰加热烧嘴方面,开发出具有还原能力的快速混合型烧嘴,并在连续镀锌线和连续退火线上得到应用。通过对烧嘴口形状、气体喷射速度和炉内热环境的设计,使快速混合型烧嘴的退火炉具有无氧化性气氛,可进行还原性加热。将这种烧嘴用于冷轧不锈钢退火炉,使退火炉高性能化,达到NOX和烟尘的环境标准规定。将这种烧嘴用做镀锌板和冷轧板连续退火的还原加热烧嘴,采用与预热空气混合燃烧的方式,预热空气最高温度达到400℃,使用的气体燃料可以是焦炉煤气或天然气。采用这种烧嘴时,不会发生分流喷射烧嘴的过热现象,当空气比小于0.8、加热到650℃以上时,炉气对钢板显示还原性。这种烧嘴在连续热镀锌的加热设备上得到应用,并达到降低能耗的效果。
在连续退火冷却技术方面,开发出高氢保护气体喷射冷却技术并形成了无氧化强冷却的新型退火冷却工艺。喷射的冷却气体的高氢化和高速化可以获得目标冷却能力,当氢浓度为60%时,冷却能力达到最大。
在连续退火过程中,来自钢板的Mn的浓聚物会沉积退火炉炉辊喷镀层上形成积瘤,炉辊积瘤又复制到钢板上,使退火钢板表面质量不良。这种现象在高强度钢板退火时更容易发生。为解决这种问题,对在炉辊喷镀材料的基体金属MCrAlY中添加陶瓷的种类和添加量进行了研究,并取得了提高抗Mn沉积性的效果。研究结果表明,MCrAlY中的Al含量越高,扩散到炉辊喷镀层内的Al量越多,在钢板上浓聚并沉积在炉辊喷镀层上的Mn量也越多。MCrAlY中添加的陶瓷量越多,扩散到炉辊喷镀层内的Al量越少,沉积的Mn量也越少。
8、冷轧和连续退火技术展望
8.1、高强钢冷轧技术展望
近年来,普通钢冷轧的硬件技术和软件技术开发有了很大进展,似乎已经达到极限的程度。在尺寸控制方面,开发出很多新技术,但在板厚精度方面停留在原有的±0.5%的水平上并没有更大的提高。此外,还有诸如轧制加、减速非正常区域的尺寸控制和轧机震动等问题。为解决这些问题必须进行进一步研发。为了制造高精度冷轧薄板,不仅要有先进的冷轧技术,同时要有提高冷轧原板热轧带卷质量的先进热轧技术,例如提高热轧带卷全长度、全宽度尺寸精度和平坦度的技术,提高热轧带卷全长度、全宽度变形抗力均匀性技术等。一般情况下,热轧钢板在热轧输送辊道上发生相变,因此需要提高冷却控制能力对相变进行精确控制。近10年来基于轧制理论的先进热轧板厚控制技术得到很大发展,今后应重点研发冷轧钢板厚度控制技术。
近10年来,没有新建具有高精度板厚控制和平坦度控制功能的新型冷轧机,平坦度控制器和尺寸精度控制器等硬件的开发也较少。平坦度控制技术的开发是在现有轧机检测装置的基础上进行的。断面尺寸形状控制和平坦度控制的综合控制系统应是今后冷轧钢板板形控制技术的开发方向,开发的重点应是数字化控制技术。从生产效率角度来看,关于坯料焊接部位(非正常部位)的高速通板问题以及该部位的尺寸和平坦度控制问题也是今后应重点研究的课题。
近10年来,对冷轧润滑的解析研究做了大量工作,今后应推进关于轧制过程中轧制油行为的研究、摩擦系数变化的研究和表面粗糙度形成机制的研究。冷轧综合润滑技术的研究开发对于产品表面性状和轧制效率的提高十分重要。在阐明冷轧过程(包括高强钢轧制)中的润滑机制和表面形成机制的同时,开发在线检测技术(粗糙度、油膜厚度)和在线控制技术是今后冷轧润滑技术和表面性状控制技术的开发方向。
关于平整轧制中表面形状形成机制问题进行了许多研究并取得了实验研究成果和FEM解析研究成果。不仅对于平整轧制,采用三元FEM数值解析技术进行冷轧板尺寸、板形、平坦度预测和轧材变形机制的研究将是今后的研究方向。
近年来,980MPa级汽车钢板的应用受到关注。串列式冷轧机组轧制高强钢板有一定的困难,在低成本高效率稳定轧制高强钢板方面还有若干问题需要解决。对于不锈钢板、电工钢板等高变形抗力钢材主要利用小辊径多辊轧机或可逆式轧机进行轧制。今后对高强钢的需求量将会增加,因此,需要进行针对高强钢的轧制工艺的研究,特别是强度超过980MPa级的超高强度钢的轧制技术还需要深入研究。
8.2、连续退火技术展望
近10年来,开发的连续退火技术中有一半是关于退火质量、生产效率和高精度温度控制的软件技术。此外,还有高速通板技术、带钢位置控制传感器等技术。喷射还原烧嘴和蓄热式辐射管烧嘴的使用对提高退火材的表面质量、节能和退火稳定性起到很大作用。对含Mn量高的高强钢进行连续退火时炉辊容易产生积瘤,因此,炉辊表面喷镀技术是今后的开发课题。为提高连续退火设备的生产效率,需要进行连续化生产,为获得规定的组织需要有自适应型温度控制功能,因此,减少因炉温、板温波动和不均匀引起的带钢通板摆动和瓢曲缺陷的技术开发是今后的重要课题。在高强钢连续退火时,控制连续退火温度曲线,可以获得规定的力学性能,因此,连续退火温度的高精度控制技术未来将越来越重要。
延伸阅读
- 上一篇:政策难以大幅提振下游钢铁需求 下一篇:5500万元弹簧项目开工