烧结用生石灰消化控制与生产参数关系的实践探索
来源:炼铁|浏览:次|评论:0条 [收藏] [评论]
烧结用生石灰消化控制与生产参数关系的实践探索彭元飞李斌严红侠(陕钢集团龙钢公司炼铁厂,陕西韩城,715405)摘 要:2019年3月至2019年10月,在265㎡烧结机通过生石灰消化时间与生产参数关…
烧结用生石灰消化控制与生产参数关系的实践探索
彭元飞 李斌 严红侠
(陕钢集团龙钢公司炼铁厂,陕西韩城,715405)
摘 要:2019年3月至2019年10月,在265㎡烧结机通过生石灰消化时间与生产参数关系的研究,形成不同的原料结构及变化及时调整关键工艺参数,明确了生石灰消化时间与生产参数数量性关系。
关键词:生石灰消化;烧结矿;参数关系
Practical exploration on the relationship between slaking control and production parameters of quicklime for sintering
Peng Yuanfei,Li Bin,Yan Hongxia
Abstract: from March 2019 to October 2019, through the research on the relationship between the slaking time and the production parameters of the 265 ㎡ sintering machine, different raw material structures and changes were formed to adjust the key process parameters in time, and the quantitative relationship between the slaking time and the production parameters was clarified.
Key words: quicklime digestion, sinter, parameter relationship
1 课题探索背景
烧结工艺是指根据原料特性所选择的加工程序和烧结工艺制度,它对烧结生产的产量和质量有着直接而重要的影响。按照烧结过程的内在规律由配料、混料、点火、抽风烧结、抽风冷却、破碎筛分,除尘等环节组成。在烧结工艺的配料、加水、混料、皮带传送、造球、一混、二混等过程中,从生石灰粉与水接触开始,或者与其他湿的原料接触开始,就开始了消化反应,直到形成料球前,此段时间内就应该完成生石灰粉的消化,否则不利,其主要原因为生石灰粉吸水后体积会膨胀两倍左右,会对料球的成球性产生一定的影响。而且,烧结工艺中的加水量要远远小于检测过程中的加水量,由此导致的是石灰消化时放出的热量能令石灰周围的原料温度有较大的提升,消化反应放出的热量在将水雾化后,再传导到其他原料上。由于料温的急剧升高,还可以促进石灰的加速消化。为此,合理控制石灰的消化时间和消化温度范围,与烧结过程相匹配,从而达到控制烧结前期的工艺效果。
2 课题研究的意义
265㎡烧结机生灰下料量结构为给料机+托带称结构,下料不稳,密封效果差,严重制约目前生产,2018年265烧结矿R稳定率为87.22%,远低于内控要求91%的目标,分析主要原因为生灰下料不稳定造成,同时存在人员调整不及时,对生石灰质量及后续生产影响认识不清造成。另外生石灰主要为外购产品,质量无法有效控制,有必要针对生石灰质量与消
化分析研究,以提升人员操作及烧结矿质量。
3 课题研究的理论依据
生石灰作为烧结生产的主要熔剂,主要有起到以下作用:作为黏结剂,可用于提高混合料的成球性;改善混合料的原始透气性,经充分与水消化后提高混合料的原始温度;调控烧结矿碱度,铁矿粉与生石灰的反应生成液相铁酸钙,形成液相的流动性直接关系到黏结相的质量,从而决定烧结矿的产量和质量。与石灰石粉等含 CaO 的熔剂相比,生石灰的高分散性和粘附性,有利于 CaO与 Fe2O3 固相反应的进行,有利于液相的形成与发展,保证烧结矿中有足够的铁酸钙生成。故有利于获得烧结矿成品率、转鼓强度、利用系数等良好的烧结指标,在烧结原料中要配入一定量的生石灰,生石灰在烧结中的作用无可替代。
4、课题研究的主要过程
2018年12月,炼铁厂为进一步优化烧结机熔剂使用,经前期论证,在265㎡烧结机开展“生石灰消化控制与生产参数关系的研究”的项目。2018年12月,成立了研究小组,并上报了该科研项目,上报公司后正式立项,该项目开展期间受到集团和公司领导的高度重视,并给予大力支持,促进本项目顺利进行。在8个月的生产过程中,充分研究了265㎡烧结机工艺控制难点,我们逐步、逐条予以解决,科研内容得到验证,至2019年10月该项目实施良好,为提高烧结超厚料层控制探索了重要途径。回顾以往,本课题主要经历了以下三个阶段:
4.1技术方案的确立
2019年3月,项目组对265㎡烧结机工艺及设备条件进行初步分析,首先确定了生产参数研究方向。
首先,物料条件多变,课题组无法周密预估生产实践中遇到问题,为了试验的顺利进行,提高方案准确性,课题组对不同原料及工艺条件下生产过程进行跟踪,并走访技术人员和生产人员,探索试验过程和方法。
第二,研究文献资料,借鉴理论经验。课题组成员终点研究近几年来国内外烧结矿质量控制研究动态,明确自身不足和新的研究方向,期间明确了研究创新点以及研究范围。
第三,对初步实施方案进行讨论。课题组根据前期走访信息及文献资料,对初步方案进行讨论,并进行修订。
4.2调整及改造方案的实施
2019年5月利用检修,对生灰给料机进行检修,发现其给料机小仓磨损严重,对原有给料机给料小仓进行修补与调整,生灰下料稳定性提升幅度较大,促进后期烧结矿R稳定率提升。配料电子秤皮带架班班清理彻底,保证计量相对准确、减小误差;固化检修期间给料机检查与修补,同时对其他称体进行校准;始终坚持三级管控和微调控制方式,确保烧结矿R稳定提升。
4.3稳定运行阶段
7月对生灰粒度进行监测,其<3mm占比逐步由90%提升至93%,烧结矿表观白点明显减少和R稳定率大幅提升,烧结料层由750mm逐步提升至830mm,垂直烧结速度由18mm/min提升至20mm/min,促进烧结机流量由540t/h提升至560t/h。
5 课题研究成果
5.1项目目标完成情况
5.1.1烧结矿R稳定率提升5%,达到≥92%。
项目实施后烧结矿R稳定率逐步提升至94%以上,均值达到92.50%,达到项目目标。
5.1.2烧结机流量提升10t/h。
项目实施后烧结流量逐步稳定至555t/h以上,均值达到559t/h,较前期540t/h提升19t/h,达到项目目标。
5.1.3形成企业生产操作规范3项。
①修订公司内控标准,纳入重点质量关注项CaO含量。
②修订265㎡烧结机参数控制标准。
③制定烧结机质量管控标准,加入生石灰消化测定要求。
5.2效益分析
根据理论“烧结矿R稳定提升10%,高炉焦比下降1%、铁水产量提升1.5%”,265㎡烧结矿R稳定提升至92.50%、较项目开展前涨幅4.26%,对高炉指标稳定提供了基础。265㎡烧结机烧结矿供应1#2#高炉,效益计算以1#2#高炉相关数据核定,其中1-6月份1#2#高炉完成焦比378kg/t、焦炭单价为1759.84元/t,7-11月1#2#高炉产量完成96.96万吨,按焦比理论下降核定效益为:4.26%/10%*1%*376*1759.84/1000*96.96=273.31万元
5.3生石灰质量与生产关系研究
5.3.1参数统计
5.3.2相关性分析
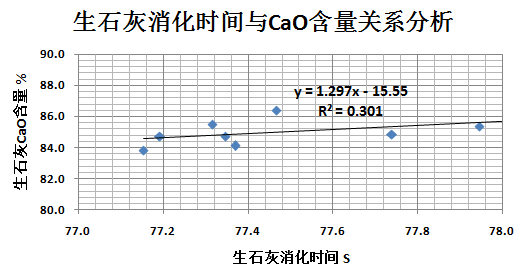
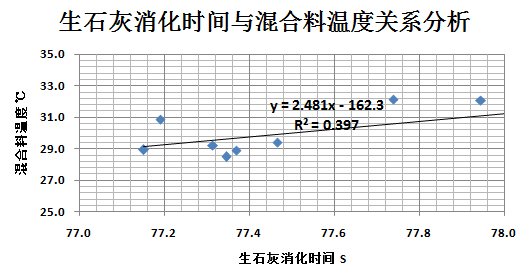
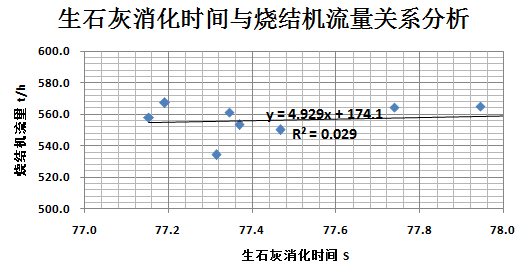
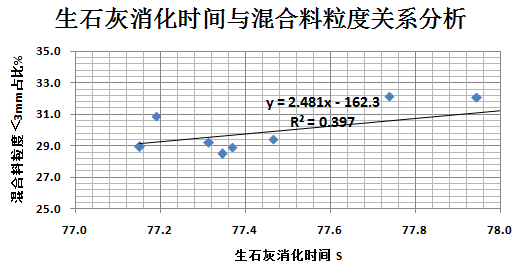
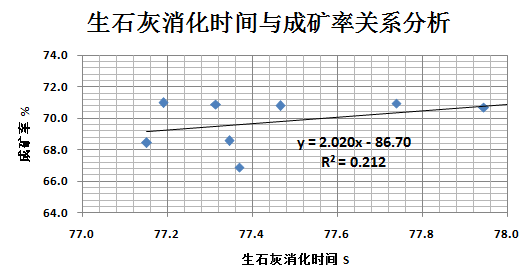
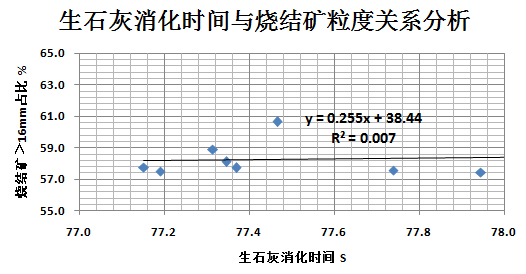
5.3.3综合分析
分析:
①生石灰消化时间为现场监测,均表现出与生产过程较大相关性。
②生石灰消化时间与CaO含量相关性达到0.549、与混合料温度相关系数0.630、与混合料粒度(<3mm)相关系数0.630、与成矿率0.460,均呈现较高相关性,对生产过程直接相关。
③生石灰消化时间与烧结机流量相关系数0.170、与烧结矿粒度相关系数0.084,呈现较弱相关性,说明其两项与生产过程其他参数相关较大。
6 课题组成员成果
6.1通过研究,逐步细化了265㎡烧结矿质量提升的工艺及设备管控思路,分厂内部形成了集中针对烧结过程中配料过程、造球过程、参数控制等方面的攻关思路,比如采取了水分控制、漏风治理、FeO优化、返矿优化、布料模式研究等重点攻关活动,促进烧结矿产质量均大幅提升。
6.2随着研究内容的逐步深入,烧结过程趋于合理,通过对生石灰消化时间研究,发现其与混合料温度、粒度、烧结机流量、烧结矿粒度组成之间的关系,提升了科研人员分析、研究、解决问题的能力,同时提升项目组成员与公司相关部门的协调沟通能力。
7 课题研究重要结论
7.1生石灰粉分散大、密度小、具有粘性,是铁矿烧结中必不可少的添加剂,烧结中添加生石灰粉能强化造粒过程,改善造粒效果,提高料球的强度,增强抗过湿能力,提高烧结混合料的原始透气性。在烧结中参与反应生成液相铁酸钙等,直接影响烧结矿强度,矿物组成和内部结构。
7.2生石灰性能不是由其用量或总氧化钙含量决定,而是由活性氧化钙含量决定,活性氧化钙含量由生石灰活性来体现。生石灰活性越高则活性氧化钙含量越高,反应性越好,越易参与烧结过程。高活性生石灰粉能显著提高烧结矿产质量。
7.3根据龙钢烧结工艺的生产特点,制定以氧化钙含量、活性度、烧损、粒度小于3 mm比例为衡量生石灰质量优劣的主要指标。质量改善后生石灰粉料切出稳定、下料顺畅,有效支撑265㎡烧结机的稳产高产和烧结矿的质量稳定。
7.4生石灰消化时间作为现场表观测定重点内容,在各烧结机配料岗位予以实施,促进烧结过程控制能力进一步提升。
彭元飞 李斌 严红侠
(陕钢集团龙钢公司炼铁厂,陕西韩城,715405)
摘 要:2019年3月至2019年10月,在265㎡烧结机通过生石灰消化时间与生产参数关系的研究,形成不同的原料结构及变化及时调整关键工艺参数,明确了生石灰消化时间与生产参数数量性关系。
关键词:生石灰消化;烧结矿;参数关系
Practical exploration on the relationship between slaking control and production parameters of quicklime for sintering
Peng Yuanfei,Li Bin,Yan Hongxia
Abstract: from March 2019 to October 2019, through the research on the relationship between the slaking time and the production parameters of the 265 ㎡ sintering machine, different raw material structures and changes were formed to adjust the key process parameters in time, and the quantitative relationship between the slaking time and the production parameters was clarified.
Key words: quicklime digestion, sinter, parameter relationship
1 课题探索背景
烧结工艺是指根据原料特性所选择的加工程序和烧结工艺制度,它对烧结生产的产量和质量有着直接而重要的影响。按照烧结过程的内在规律由配料、混料、点火、抽风烧结、抽风冷却、破碎筛分,除尘等环节组成。在烧结工艺的配料、加水、混料、皮带传送、造球、一混、二混等过程中,从生石灰粉与水接触开始,或者与其他湿的原料接触开始,就开始了消化反应,直到形成料球前,此段时间内就应该完成生石灰粉的消化,否则不利,其主要原因为生石灰粉吸水后体积会膨胀两倍左右,会对料球的成球性产生一定的影响。而且,烧结工艺中的加水量要远远小于检测过程中的加水量,由此导致的是石灰消化时放出的热量能令石灰周围的原料温度有较大的提升,消化反应放出的热量在将水雾化后,再传导到其他原料上。由于料温的急剧升高,还可以促进石灰的加速消化。为此,合理控制石灰的消化时间和消化温度范围,与烧结过程相匹配,从而达到控制烧结前期的工艺效果。
2 课题研究的意义
265㎡烧结机生灰下料量结构为给料机+托带称结构,下料不稳,密封效果差,严重制约目前生产,2018年265烧结矿R稳定率为87.22%,远低于内控要求91%的目标,分析主要原因为生灰下料不稳定造成,同时存在人员调整不及时,对生石灰质量及后续生产影响认识不清造成。另外生石灰主要为外购产品,质量无法有效控制,有必要针对生石灰质量与消
化分析研究,以提升人员操作及烧结矿质量。
3 课题研究的理论依据
生石灰作为烧结生产的主要熔剂,主要有起到以下作用:作为黏结剂,可用于提高混合料的成球性;改善混合料的原始透气性,经充分与水消化后提高混合料的原始温度;调控烧结矿碱度,铁矿粉与生石灰的反应生成液相铁酸钙,形成液相的流动性直接关系到黏结相的质量,从而决定烧结矿的产量和质量。与石灰石粉等含 CaO 的熔剂相比,生石灰的高分散性和粘附性,有利于 CaO与 Fe2O3 固相反应的进行,有利于液相的形成与发展,保证烧结矿中有足够的铁酸钙生成。故有利于获得烧结矿成品率、转鼓强度、利用系数等良好的烧结指标,在烧结原料中要配入一定量的生石灰,生石灰在烧结中的作用无可替代。
4、课题研究的主要过程
2018年12月,炼铁厂为进一步优化烧结机熔剂使用,经前期论证,在265㎡烧结机开展“生石灰消化控制与生产参数关系的研究”的项目。2018年12月,成立了研究小组,并上报了该科研项目,上报公司后正式立项,该项目开展期间受到集团和公司领导的高度重视,并给予大力支持,促进本项目顺利进行。在8个月的生产过程中,充分研究了265㎡烧结机工艺控制难点,我们逐步、逐条予以解决,科研内容得到验证,至2019年10月该项目实施良好,为提高烧结超厚料层控制探索了重要途径。回顾以往,本课题主要经历了以下三个阶段:
4.1技术方案的确立
2019年3月,项目组对265㎡烧结机工艺及设备条件进行初步分析,首先确定了生产参数研究方向。
首先,物料条件多变,课题组无法周密预估生产实践中遇到问题,为了试验的顺利进行,提高方案准确性,课题组对不同原料及工艺条件下生产过程进行跟踪,并走访技术人员和生产人员,探索试验过程和方法。
第二,研究文献资料,借鉴理论经验。课题组成员终点研究近几年来国内外烧结矿质量控制研究动态,明确自身不足和新的研究方向,期间明确了研究创新点以及研究范围。
第三,对初步实施方案进行讨论。课题组根据前期走访信息及文献资料,对初步方案进行讨论,并进行修订。
4.2调整及改造方案的实施
2019年5月利用检修,对生灰给料机进行检修,发现其给料机小仓磨损严重,对原有给料机给料小仓进行修补与调整,生灰下料稳定性提升幅度较大,促进后期烧结矿R稳定率提升。配料电子秤皮带架班班清理彻底,保证计量相对准确、减小误差;固化检修期间给料机检查与修补,同时对其他称体进行校准;始终坚持三级管控和微调控制方式,确保烧结矿R稳定提升。
4.3稳定运行阶段
7月对生灰粒度进行监测,其<3mm占比逐步由90%提升至93%,烧结矿表观白点明显减少和R稳定率大幅提升,烧结料层由750mm逐步提升至830mm,垂直烧结速度由18mm/min提升至20mm/min,促进烧结机流量由540t/h提升至560t/h。
5 课题研究成果
5.1项目目标完成情况
5.1.1烧结矿R稳定率提升5%,达到≥92%。
月份 | 2019.3 | 2019.4 | 2019.5 | 2019.6 | 2019.7 | 2019.8 | 2019.9 | 2019.10 | 2019.11 |
烧结矿R稳定率 % | 87.98 | 88.49 | 89.46 | 89.53 | 92.56 | 94.50 | 88.28 | 94.66 | 95.49 |
阶段均值 | 88.24 | 89.50 | 92.50 | 95.49 | |||||
阶段 | 理论研究 | 调整期 | 稳定运行 | 后期 |
5.1.2烧结机流量提升10t/h。
月份 | 2019.3 | 2019.4 | 2019.5 | 2019.6 | 2019.7 | 2019.8 | 2019.9 | 2019.10 | 2019.11 |
烧结机流量 t/h | 553 | 555 | 561 | 542 | 550 | 555 | 565 | 567 | 564 |
阶段均值 | 554 | 552 | 559 | 564 | |||||
阶段均值 | 理论研究 | 调整期 | 稳定运行 | 后期 |
5.1.3形成企业生产操作规范3项。
①修订公司内控标准,纳入重点质量关注项CaO含量。
②修订265㎡烧结机参数控制标准。
③制定烧结机质量管控标准,加入生石灰消化测定要求。
5.2效益分析
根据理论“烧结矿R稳定提升10%,高炉焦比下降1%、铁水产量提升1.5%”,265㎡烧结矿R稳定提升至92.50%、较项目开展前涨幅4.26%,对高炉指标稳定提供了基础。265㎡烧结机烧结矿供应1#2#高炉,效益计算以1#2#高炉相关数据核定,其中1-6月份1#2#高炉完成焦比378kg/t、焦炭单价为1759.84元/t,7-11月1#2#高炉产量完成96.96万吨,按焦比理论下降核定效益为:4.26%/10%*1%*376*1759.84/1000*96.96=273.31万元
5.3生石灰质量与生产关系研究
5.3.1参数统计
月份 | 流量 t/h |
熔剂单耗 kg/t |
利用系数 t/㎡h |
出厂矿 万吨 |
成矿率 % |
R稳定率 % |
混合料<3mm % |
台车料温 ℃ |
生石灰CaO % |
生石灰<3mm % |
消化时间 S |
烧结矿>16mm % |
平均粒径 mm |
2019.3 | 553 | 156.64 | 1.41 | 17.36 | 66.85 | 87.98 | 28.89 | 52.9 | 84.10 | 89.61 | 77.37 | 57.71 | 21.40 |
2019.4 | 558 | 164.23 | 1.44 | 20.49 | 68.41 | 88.49 | 28.91 | 55.7 | 83.82 | 89.75 | 77.15 | 57.73 | 21.53 |
2019.5 | 561 | 145.70 | 1.44 | 18.36 | 68.54 | 89.46 | 28.46 | 58.2 | 84.69 | 89.96 | 77.35 | 58.08 | 21.43 |
2019.6 | 534 | 149.48 | 1.44 | 18.14 | 70.86 | 89.53 | 29.20 | 63.3 | 85.47 | 89.91 | 77.31 | 58.86 | 21.33 |
2019.7 | 550 | 153.85 | 1.47 | 19.24 | 70.77 | 92.56 | 29.38 | 64.1 | 86.39 | 89.78 | 77.47 | 60.62 | 21.72 |
2019.8 | 555 | 146.16 | 1.49 | 19.04 | 71.16 | 94.50 | 30.62 | 63.1 | 85.98 | 89.14 | 78.18 | 58.93 | 21.34 |
2019.9 | 565 | 145.71 | 1.50 | 19.55 | 70.67 | 88.28 | 32.05 | 62.8 | 85.36 | 88.98 | 77.94 | 57.43 | 21.32 |
2019.10 | 567 | 145.35 | 1.51 | 18.61 | 70.95 | 94.66 | 30.83 | 61.3 | 84.73 | 90.16 | 77.19 | 57.47 | 21.27 |
2019.11 | 564 | 150.44 | 1.51 | 17.90 | 70.93 | 95.49 | 32.13 | 60.3 | 84.83 | 90.50 | 77.74 | 57.55 | 21.68 |
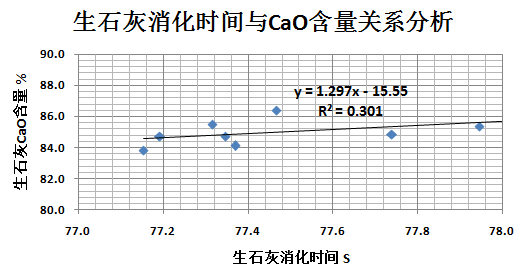
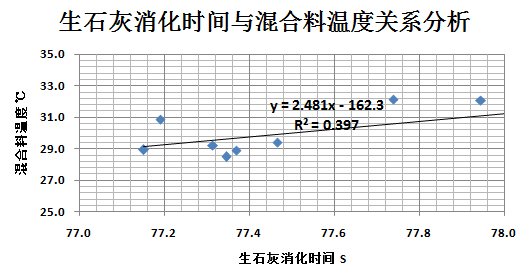
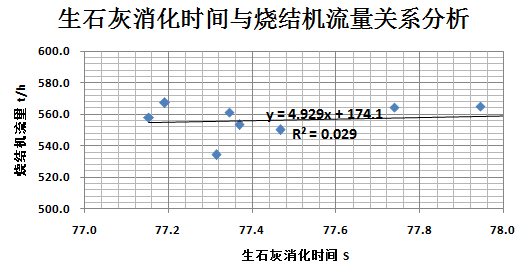
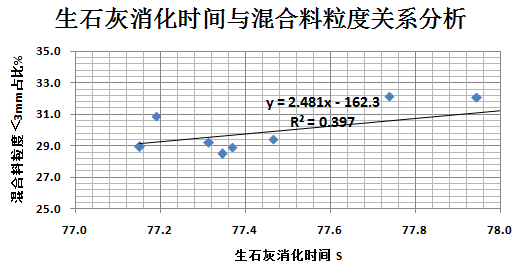
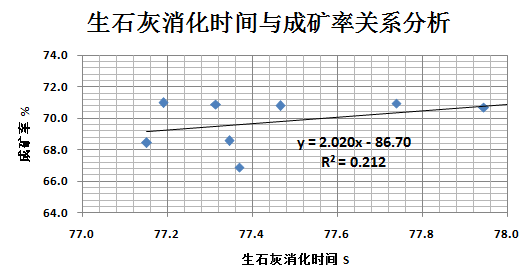
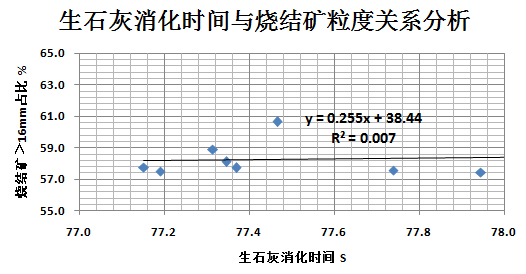
5.3.3综合分析
项目 | 关系式 | R² | 相关性 |
与CaO含量关系 | y=1.297x-15.55 | 0.301 | 0.549 |
与混合料温度关系 | y=2.481x-62.3 | 0.397 | 0.630 |
与烧结机流量关系 | y=4.929x+174.1 | 0.029 | 0.170 |
与混合料粒度关系(<3mm) | y=2.481x-162.3 | 0.397 | 0.630 |
与成矿率关系 | y=2.020x-86.70 | 0.212 | 0.460 |
与烧结矿粒度关系 (>16mm) |
y=0.255x+38.44 | 0.007 | 0.084 |
①生石灰消化时间为现场监测,均表现出与生产过程较大相关性。
②生石灰消化时间与CaO含量相关性达到0.549、与混合料温度相关系数0.630、与混合料粒度(<3mm)相关系数0.630、与成矿率0.460,均呈现较高相关性,对生产过程直接相关。
③生石灰消化时间与烧结机流量相关系数0.170、与烧结矿粒度相关系数0.084,呈现较弱相关性,说明其两项与生产过程其他参数相关较大。
6 课题组成员成果
6.1通过研究,逐步细化了265㎡烧结矿质量提升的工艺及设备管控思路,分厂内部形成了集中针对烧结过程中配料过程、造球过程、参数控制等方面的攻关思路,比如采取了水分控制、漏风治理、FeO优化、返矿优化、布料模式研究等重点攻关活动,促进烧结矿产质量均大幅提升。
6.2随着研究内容的逐步深入,烧结过程趋于合理,通过对生石灰消化时间研究,发现其与混合料温度、粒度、烧结机流量、烧结矿粒度组成之间的关系,提升了科研人员分析、研究、解决问题的能力,同时提升项目组成员与公司相关部门的协调沟通能力。
7 课题研究重要结论
7.1生石灰粉分散大、密度小、具有粘性,是铁矿烧结中必不可少的添加剂,烧结中添加生石灰粉能强化造粒过程,改善造粒效果,提高料球的强度,增强抗过湿能力,提高烧结混合料的原始透气性。在烧结中参与反应生成液相铁酸钙等,直接影响烧结矿强度,矿物组成和内部结构。
7.2生石灰性能不是由其用量或总氧化钙含量决定,而是由活性氧化钙含量决定,活性氧化钙含量由生石灰活性来体现。生石灰活性越高则活性氧化钙含量越高,反应性越好,越易参与烧结过程。高活性生石灰粉能显著提高烧结矿产质量。
7.3根据龙钢烧结工艺的生产特点,制定以氧化钙含量、活性度、烧损、粒度小于3 mm比例为衡量生石灰质量优劣的主要指标。质量改善后生石灰粉料切出稳定、下料顺畅,有效支撑265㎡烧结机的稳产高产和烧结矿的质量稳定。
7.4生石灰消化时间作为现场表观测定重点内容,在各烧结机配料岗位予以实施,促进烧结过程控制能力进一步提升。
延伸阅读
- 上一篇:降低燃料消耗生产实践 下一篇:龙钢400㎡烧结机超厚料层生产实践