首钢京唐板坯连铸技术进步
浏览:次|评论:0条 [收藏] [评论]
首钢京唐板坯连铸技术进步陈凌峰1), 赵长亮1), 邓小旋2), 季晨曦1,2)(1 首钢京唐钢铁联合有限责任公司,河北唐山063200;2 首钢集团有限公司技术研究院,北京100043)1)摘 要:本文…
首钢京唐板坯连铸技术进步
陈凌峰1), 赵长亮1), 邓小旋2), 季晨曦1,2)
(1.首钢京唐钢铁联合有限责任公司,河北唐山 063200; 2.首钢集团有限公司技术研究院,北京 100043)
1)摘 要:本文回顾了近十年来首钢京唐为生产优质冷轧钢板和特厚钢板而开发的板坯连铸新技术。为了降低优质冷轧钢板表面冶金缺陷,开发了浸入式水口防堵塞技术、结晶器内钢液流动综合控制技术和中高拉速FC结晶器技术等。综合应用这些技术后,水口堵塞率降低60%以上,结晶器液面波动±3mm比例提高至98%以上,冷轧钢板表面卷渣缺陷指数降低了50%以上。通过倒角结晶器内流动传热模拟研究、矫直过程应力应变模拟研究、结晶器铜板温度分布研究,提出了具有自主知识产权的带有圆管式附加冷却孔的大倒角结晶器窄面铜板,将全钢种轧材边部缺陷率<0.4%。并自主开发、完善10余项铸机自动化功能,改善了现场工作环境,降低了职工劳动量。单台铸机人员数量由原来的13人/铸机降低至目前的6人/铸机。
关键词:水口堵塞;卷渣;结晶器流场控制;高拉速;倒角结晶器;无人化浇铸
Progresses of Slab Continuous Casting Technology Development at Shougang Jingtang
CHEN Ling-feng1), ZHAO Chang-liang 1), DENG Xiao-xuan2), JI Chen-xi1,2)
(1.Shougang Jingtang Iron & Steel Co.,LTD ; 2.Research Institute of Technology, Shougang Group Co., Ltd, Beijing, 100043, China )
Abstract: Progresses of developed continuous casting technology to produce high quality cold rolled sheets and heavy plates during last ten years were reviewed in this paper. In order to minimize the metallurgical surface defects of high quality cold rolled sheets, several technologies were developed including clogging prevention of submerged entry nozzle, optimization and control of flow pattern in CC mold, optimization of FC mold under medium-high speed CC. The ratio of SEN clogging was reduced above 60%. The time percentage of fluctuation of mold level within ±3mm is higher than 98%. The index of surface defects caused by entrapped mold powder was reduced more than 50%. Through the simulation study of flow heat transfer in the chamfered mold, stress-strain simulation of the straightening process, and temperature distribution calculation of the copper plate of the mold, a large chamfered mold technology with circular tube type additional cooling holes is proposed. The edge defect rate of the coils is controlled <0.4%. And more than 10 casting machine automation functions were developed independently , improving the on-site working environment and reducing the workload of employees. Employees of single casters have been reduced from the original 13/caster to the 6/caster.
Keyword: SEN clogging; mold powder entrapment; flow control in the mold; high speed; chamfered mold;
关键词:水口堵塞;卷渣;结晶器流场控制;高拉速;倒角结晶器;无人化浇铸
Progresses of Slab Continuous Casting Technology Development at Shougang Jingtang
CHEN Ling-feng1), ZHAO Chang-liang 1), DENG Xiao-xuan2), JI Chen-xi1,2)
(1.Shougang Jingtang Iron & Steel Co.,LTD ; 2.Research Institute of Technology, Shougang Group Co., Ltd, Beijing, 100043, China )
Abstract: Progresses of developed continuous casting technology to produce high quality cold rolled sheets and heavy plates during last ten years were reviewed in this paper. In order to minimize the metallurgical surface defects of high quality cold rolled sheets, several technologies were developed including clogging prevention of submerged entry nozzle, optimization and control of flow pattern in CC mold, optimization of FC mold under medium-high speed CC. The ratio of SEN clogging was reduced above 60%. The time percentage of fluctuation of mold level within ±3mm is higher than 98%. The index of surface defects caused by entrapped mold powder was reduced more than 50%. Through the simulation study of flow heat transfer in the chamfered mold, stress-strain simulation of the straightening process, and temperature distribution calculation of the copper plate of the mold, a large chamfered mold technology with circular tube type additional cooling holes is proposed. The edge defect rate of the coils is controlled <0.4%. And more than 10 casting machine automation functions were developed independently , improving the on-site working environment and reducing the workload of employees. Employees of single casters have been reduced from the original 13/caster to the 6/caster.
Keyword: SEN clogging; mold powder entrapment; flow control in the mold; high speed; chamfered mold;
前言
自2002年开始,首钢集团实施了搬迁调整,将产品结构由长材为主调整为优质板材。在曹妃甸京唐公司建成4台板坯连铸机,主要用于生产汽车板、镀锡板、家电板和车轮钢等薄板产品。在冷轧钢板的表面缺陷中,主要的冶金缺陷有线状缺陷、翘皮、气泡和孔洞,这些都与连铸工序密切相关[1-4]。如:簇群状Al2O3会在冷轧钢板表面形成灰白色线状缺陷,卷入的保护渣会造成灰黑色线状缺陷,气泡+Al2O3会造成翘皮缺陷等。因此,防止水口堵塞、降低结晶器液面波动和控制结晶器流场等技术成为控制这些缺陷的主要措施。同时,针对板坯的角横裂问题,开发了倒角结晶器技术。并自主开发、完善铸机自动化功能,以降低工艺操作难度、提高生产效率和铸坯质量,同时改善现场工作环境,降低职工劳动量。1板坯连铸技术进步
1.1浸入式水口防堵塞技术
冷轧钢板主要采用Al脱氧,脱氧产物或者二次氧化生成的Al2O3是浸入式水口堵塞的主要原因。为了减轻水口堵塞,普遍采用的技术措施有:1)综合运用洁净钢冶炼的各种技术,提高精炼结束时钢水的洁净度,严格控制钢水总氧含量至较低水平;2)严格保护浇注,如钢包长水口浸入式开浇、中间包上水口、塞棒(或滑板间)、浸入式水口吹氩等。采用上述技术措施后,还存在以下两个问题:一是在浇铸过程尤其是换包过程中包液面出现 “渣眼”,即钢水裸露,这很容易造成钢水二次氧化,从而导致水口发生堵塞,塞棒棒位快速上涨,连浇被迫中断;二是方形浸入式水口的出口上沿存在低速流区,堵塞物容易在此聚集。为了解决这些问题,本项目开发了长水口“渣眼”抑制技术和椭圆形浸入式水口技术。
对安装湍流抑制器的中间包进行了数值模拟,发现长水口“渣眼”的形成原因是:钢水自水口流出后,冲击至湍流抑制器底部,形成很强的反向流股,该流股直冲至中间包钢液表面,在长水口附近形成“渣眼”,如图1(a)所示。因此,湍流抑制器优化的方向是将钢水冲击的能量耗散在湍流抑制器内部,确保反向流股不冲击钢水液面,使中包钢水始终被覆盖剂所覆盖。采用新型湍流抑制器后钢液的流动见图1(b)。该湍流抑制器应用后,整个浇次不再出现“渣眼”问题,中间包内钢水的二次氧化得到了有效控制,中间包总氧含量降低3ppm左右。
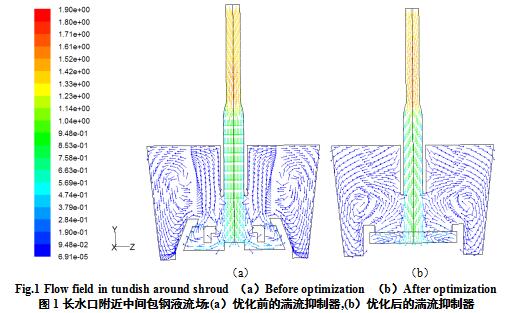
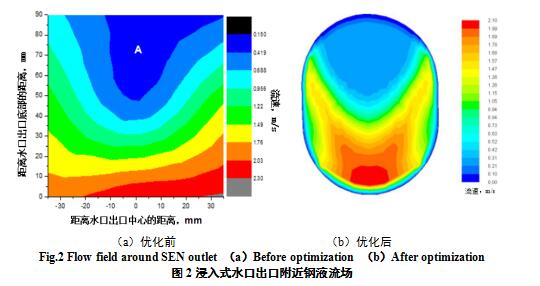
1.2结晶器内钢液流动综合控制技术
结晶器保护渣卷入受钢液流动形态的影响很大。大量的水模型研究[5-8]发现:结晶器内钢液流动呈现双股流模式,即钢液从水口流出后,形成一股很强的射流,撞击到结晶器窄面后(距离弯月面约400mm,与浸入式水口的角度和插入深度有关),射流才改变方向,分成向上和向下两股钢流。向上的流股在自由表面附近形成两个较强回流,该回流会促进夹杂物的上浮并影响自由表面的波动。向下的流股也形成与上部回流方向相反、范围更大的两个回流,其强度在向下延伸时逐渐减弱。双股流动模式有利于提高钢水弯月面温度,促进保护渣熔化。图3(a)展示了1:1水模型实验中典型双股流模式,宏观流态见图中手绘线所示。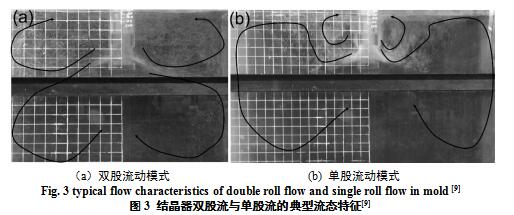
为了缓解浸入式水口堵塞,普遍采用塞棒、上水口和浸入式水口吹氩技术。但是,随着吹氩量的增加,结晶器内钢液的流场形态会发生明显的变化:上回流增强,涡心位置向结晶器表面和浸入式水口侧移动;下回流减弱,冲击深度降低。当吹氩量超过某临界值时,流动模式会转化为单股流动模式,如图3(b)所示。与图3(a)的流场完全不同,钢水流携带气泡从水口吐出后,大量气泡伴随着钢水流往结晶器液面中心运动,一部分在结晶器中部形成两股近乎垂直的上冲流,另一部分气泡和钢水朝窄面运行,到达窄面后向下折返形成一个大环流。向上的冲流会导致结晶器液面波动加剧,对保护渣的剪切力增大。研究表明:单股流的流场形态对卷渣有非常不利的影响[10-12]。不仅如此,宽断面冷轧钢板表面卷渣的发生率高于常规宽度,而相关的连铸工艺参数及保护渣未发生变化。该问题是否与单流股相关也需要开展研究。
为了避免单股流模式所带来的危害,采用水模型和插钉法研究了不同拉速、断面条件下,保证结晶器双股流的临界吹氩量,如图4所示。可见,1)临界吹氩量随通钢量的增加而增大。以1300mm宽度为例,当通钢量为3.5t/min,即拉速为1.5m/min时,临界吹氩量为8L/min。2)相同通钢量条件下,随之断面宽度的增加,临界吹氩量迅速降低。当通钢量为3.5t/min时,与1050mm断面相比,1900mm断面临界吹氩量降低了约40%。采用临界吹气量控制策略后,结晶器内翻腾现象基本解决,消除了结晶器翻腾导致的卷渣。
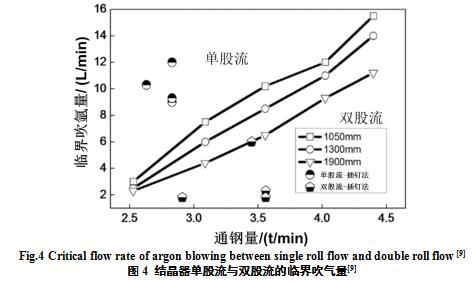
1.3 中高拉速下FC结晶器技术
FC-mold是由两个覆盖整个板坯宽度的水平磁场构成。一段磁场放置在弯月面处,目的是为了降低弯月面处的钢液流速。另一段磁场施加在浸入式水口下方,降低结晶器主流股对窄面的冲击速度[13]。其主要用于高拉速(≥1.8m/min)下结晶器内钢液流动的控制,当拉速低于1.8m/min时,投入FC结晶器反而增加了卷渣发生概率。为了建立高效化的生产工艺流程,实现炼钢、精炼以及连铸的匹配,对于断面在1300mm以下时,需要将拉速提高至1.5-1.7m/min。在此拉速下,结晶器液面波动明显增加,冷轧钢板表面卷渣缺陷指数也随之增加,因此,有必要开发中高拉速下FC结晶器技术。
图5给出了FC结晶器上部线圈电流对冷轧钢板表面卷渣缺陷指数的影响。实验条件为:拉速1.6m/min、断面宽度1300mm、下部线圈电流542A,上部线圈电流在0-450A之间变化。可见,1)与没有应用FC-mold技术相比,即便是上部线圈的电流为0,卷渣缺陷指数下降了约40%。主要原因是下部磁场在降低钢液撞击到窄面的速度的基础上,降低了向上反流的速度,从而减少了液面波动。插钉法测定的结晶器内钢液流动的波形显示,没有应用FC-mold时,液面波峰波谷差达到30mm以上,使用电流组合为 0/542A后,结晶器液面波峰波谷差缩小至15mm左右,降低了约50%。2)当上部线圈电流增加至50-150A时,卷渣缺陷指数降低了50%以上,插钉法测定的结晶器液面波峰与波谷的差值在10mm以下。3)随之上部线圈电流进一步增大,卷渣发生率增加。其主要原因是结晶器内钢液流动转变为单股流,插钉法显示,在宽度1/4处,结晶器表面钢液流速指向窄面。
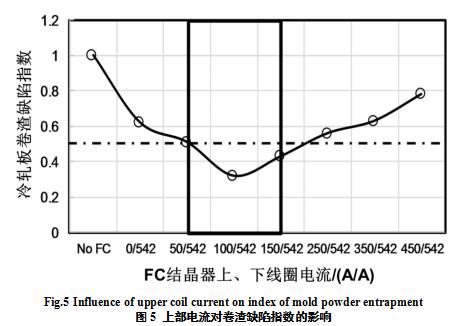
在综合浸入式水口角度、插入深度、结晶器断面和拉速优化的基础上,成功开发了中高拉速下FC结晶器技术,实现了1.5-1.7m/min拉速下FC结晶器的常态化应用,在有效抑制结晶器液面波动的同时,将钩状坯壳深度从2.3mm降低至1.7mm,有效地降低了卷渣缺陷。使用FC mold对钩状坯壳影响见图6所示。
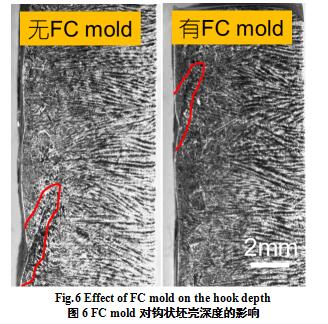
1.4倒角结晶器技术
连铸板坯角横裂纹缺陷是微合金化钢板坯的主要表面缺陷。其主要原因是角部二维传热使板坯角部温度在连铸弯曲或矫直过程落入钢种的第三脆性区,导致应力开裂[14]。传统控制板坯角横裂纹的方式是优化结晶器振动方式和二冷制度等,但无法从根源上消除此缺陷。倒角结晶器技术的主要思路是将板坯角部的传热状态由二维改为一维,提高角部温度。针对首钢京唐公司板坯连铸微合金化钢中所存在的角部横裂纹发生率高的问题,采用大倒角结晶器技术对现有连铸工艺优化改进,从结晶器传热均匀性及铸坯凝固过程角度出发,分析了铸坯角横裂的形成机理,通过倒角结晶器内流动传热模拟研究、矫直过程应力应变模拟研究、结晶器铜板温度分布研究,确定了铸坯角部倒角角度、倒角部长度及倒角面冷却结构,提出了具有自主知识产权的带有圆管式附加冷却孔的大倒角结晶器窄面铜板,其横截面结构示意图如图7所示。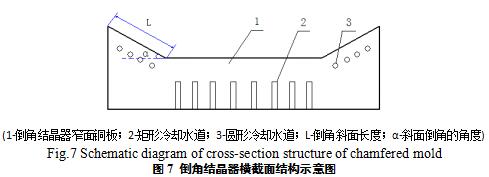
采用倒角结晶器技术生产钢种包括低碳、超低碳钢,石油管线钢(X80、X65、X60、X52),石油套管钢(J55),Q345B、Q345qc,SS400、SS400加硼,高强机械用钢、船板钢等20多个钢种。铸机正常生产微合金化钢的拉速为1.0~1.4m/min。对所生产的662块(约占总生产量的三分之一)带倒角的连铸坯进行清理检查,结果无一块铸坯存在角部横裂、纵裂缺陷。对全部带倒角连铸坯进行轧制后,轧材边部缺陷率<0.4%。
1.5连铸无人化智能浇铸平台
进入21世纪,板坯连铸自动化控制技术又有了长足进步,京唐公司以工艺、操作需求为前提,自主开发、完善10余项铸机自动化功能,实现了中包无人值守浇注;开发了浇铸系统智能语音自动报警及智能事故处理系统,不仅降低了工艺操作难度、提高了生产效率和铸坯质量,同时改善了现场工作环境,降低了职工劳动量。单台铸机人员数量由原来的13人/铸机降低至目前的6人/铸机,各岗位均达到浦项光阳厂单台铸机人员数量水平。
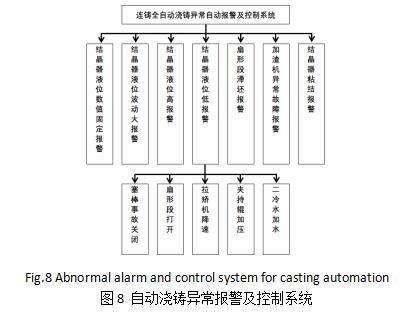
3结论
为了满足优质板材对冶金质量的要求,介绍了过去十年在连铸技术上取得的进步,主要结论有:1)针对优质冷轧钢板表面冶金缺陷,开发了浸入式水口防堵塞技术、结晶器内钢液流动综合控制技术和中高拉速下FC结晶器技术等,实现了水口堵塞率降低60%以上,结晶器液面波动±3mm比例提高至98%以上,冷轧钢板表面卷渣缺陷指数降低了50%左右。
2)通过倒角结晶器内流动传热模拟研究、矫直过程应力应变模拟研究、结晶器铜板温度分布研究,提出了具有自主知识产权的带有圆管式附加冷却孔的大倒角结晶器窄面铜板,将全钢种轧材边部缺陷率<0.4%。
3)在以工艺、操作需求为前提,自主开发、完善10余项铸机自动化功能,改善了现场工作环境,降低了职工劳动量。单台铸机人员数量由原来的13人/铸机降低至目前的6人/铸机。
参考文献
[1] 朱国森,王新华,邓小旋,等. 非稳态连铸坯洁净度的定量研究[J]. 炼钢, 2013, 29(6):41.
[2] 王新华. 高品质冷轧薄板钢中非金属夹杂物控制技术[J]. 钢铁, 2013, 48(9): 1.
[3] Miki Y, Takeuchi J, Thomas B. Internal defects of continuous casting slabs caused by asymmetric unbalanced steel flow in mold[J]. ISIJ International, 2003, 43(10):1548.
[4] 张乔英,王立涛,王新华. 非稳态浇铸条件下IF钢铸坯表层夹杂物粒径分布规律[J]. 特殊钢,2006, 27(5): 9
[5] 雷洪,朱苗勇,邱同榜.板坯连铸结晶器流场优化[J]. 炼钢,2000,16(3):29.
[6] 陈永范,陈德杰,李权.大板坯连铸结晶器内流场实验研究[J]. 炼钢,1998(2):25.
[7] Thomas B G,Mika L J,Najjar F M.Simulation of Fluid Flow inside a Continuous Slab-Casting Machine [J]. Metallurgical and Materials Transactions B,1990(21B):387.
[8] GuptaD,LahiriAK.Water-Modeling Study of the Surface Disturbances in Continuous Slab Caster [J]. Metallurgical and Materials Transactions B,1994(25B):227.
[9]邓小旋, 季晨曦, 崔阳, 等.吹氩板坯连铸结晶器内钢水流态[J].钢铁, 2016, 51(10), 23-30.
[10] AndrzejewskiP, KohlerKU, and PluschkellW.Model Investigations on the Fluid Flow in Continuous Casting Moulds of Wide Dimensions [J]. Steel Research, 1992, 63(6):242.
[11] Assar M B, Dauby P H, Lawson G D. Opening the black box: PIV and MFC measurements in a continuous caster mold. 83rd Steelmaking Conference, 2000:397.
[12] Deng X, Ji C, Cui Y, et al.Flow pattern control in continuous slab casting moulds: physical modelling and plant trials[J]. Ironmaking Steelmaking, 2017, 44(6):461.
[13] Li L, Wang X, Deng X, et al. Application of High Speed Continuous Casting on Low Carbon Conventional Slab in SGJT[J].Steel Research International,2014, 85 (11): 1490.
[14]Yasunaka H, Nakayama K, Ebina K, et al. Improvement of Transverse Corner Cracks in Continuously Cast Hypoperitectic Slabs[J].Tetsu-to-Hagane, 1995, 81(9):894.
延伸阅读
- 上一篇:炼钢脱氧剂辅料的发展技术与实践 下一篇:中天钢铁一烧结高碱度烧结生产实践