大断面矩形结晶器铜管使用过程中变形分析
来源:2019全国高效连铸应用技术及铸坯质量控制研讨会论文集|浏览:次|评论:0条 [收藏] [评论]
大断面矩形结晶器铜管使用过程中变形分析韩伦杰1 曹学谦2(1钢铁研究总院华东分院 2中冶京诚)摘要:首先简要论述了矩形结晶器在浇注过程铜管的受力机理,然后对大断面矩形铜管,在承受不同…
大断面矩形结晶器铜管使用过程中变形分析
韩伦杰1 曹学谦2
(1钢铁研究总院华东分院 2中冶京诚)
摘要:首先简要论述了矩形结晶器在浇注过程铜管的受力机理,然后对大断面矩形铜管,在承受不同水压状态下进行测量,分析了结晶器铜管在冷却水压力作用下,铜管锥度的变化。同时进行建立数模,进行模拟计算,得出相同的结果。为结晶器铜管设计、浇注过程的合理使用提供了依据。(1钢铁研究总院华东分院 2中冶京诚)
关键词:矩形结晶器,铜管,冷却水压,热应力,变形,锥度
0. 引言
结晶器铜管作为连铸的核心部件,铜管锥度合适与否,直接影响到连铸坯的质量与浇注过程的顺行。分析清楚结晶器铜管在浇注状态时的受力状况,有利于更加深入地了解铸坯在结晶器产生各种缺陷的原因、机理,同时在铜管设计过程中也能够充分考虑与应用。随着大断面矩形结晶器铜管的普遍使用,其在浇注状态的内腔尺寸的变化,直接影响到浇钢产品的质量。
1. 受力分析与理论计算
1.1. 结晶器铜管在浇注过程的受力分析
在浇注过程中,铜管的受力状态如下图:
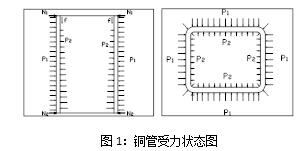
N1、N2:铜管密封预紧力;
P1:铜管冷却水静压力;
P2:钢水的静压力;
f:拉钢过程的摩擦力;
从上图可以看出,铜管除安装密封时,受所需的压力外,由于铜管外壁冷却,一定的水流速,承受冷却水压力、钢水的静压力、拉钢过程的摩擦力。
冷却水对铜管产生的静压力:
P1﹦Pw+Ph
式中:Pw 冷却水静压力对铜管产生的力;
Ph 由于结晶器冷却水高度差,对铜管产生的压力;
一般情况下, Ph仅为Pw的1/100左右,在试验与计算中可以不予考虑。
钢水对铜管产生的静压力为:
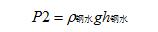
ρ钢水为ρ水的6.8 ~7.3倍,在结晶器内的h钢水最大值为720mm(结晶器总长为800mm),产生的压力约为0.05MPa,即使全部作用在铜管上(不考虑坯壳承受部分钢水静压力),与结晶器冷却水产生的压力0.6~1.0MPa相比,仍有较大的差距,故在试验与计算过程中不考虑钢水对铜管产生的压力。
铜管受热不均匀产生的应力:
在浇注过程,由于铜管热负荷主要集中在弯月面及以下300mm以内,内外壁受热不均匀,也使铜管产生一定的变形。
1.2. 理论计算
1.2.1. 未浇注态状况
在结晶器未进行浇注,提供正常的结晶器冷却水量情况下,由于铜管冷却过程水压的作用,铜管内壁会发生微量的变形。其变形量的多少直接影响到浇注过程的铸坯质量、铜管的制作与改进。为此先按照理论机械计算,承压后铜管的变形量。
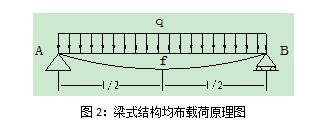
在一个梁式结构件两端固定时,给一个相对均匀分布的压力(液态均布压强作用下),结构件会有一定的变形,中心部位变形量最大,称为挠度(如图2)。铜管变形按照这种模型进行理论计算,材质为纯铜,计算370*480铜管宽面的变形量如下表:
表1:铜材梁式结构理论挠度表
名称 | 冷却水压力MPa | 宽面长度m | 铜管壁厚mm | 理论单侧最大挠度(mm) |
1 | 0.6 | 0.492 | 32 | 1.3097 |
2 | 1.0 | 0.492 | 32 | 2.1828 |
3 | 0.6 | 0.380 | 32 | 0.4661 |
4 | 1.0 | 0.380 | 32 | 0.7768 |
1.2.2. 浇注过程状况
在浇注过程中,铜管内外壁有一定的温度差,也使铜管产生微量的变形。由于结晶器的弯月面与其他部位的传热量的差别,内外壁的温差为不均匀分布。但总体为铜管内壁温度高于外壁温度,使铜管有微量的向内鼓胀趋势。
计算简化为:铜管内外壁温差按照100℃计算,纯铜的热膨胀系数为16.7×10-6m/℃,由于受结晶器角部的约束,结晶器宽、窄面变形量计算如下:
结晶器宽面变形量为:
16.7×10-6×100×0.48=8.016×10-4m=0.8016mm
结晶器窄面变形量为:
16.7×10-6×100×0.37=6.179×10-4m=0.6179mm
从以上分析看:结晶器铜管冷却水压的影响应大于结晶器热负荷造成的影响。下面对结晶器冷却水压对铜管变形的进行测量与分析。
2. 试验检测与分析
对370*480铜管(壁厚32mm)的不同部位进行检测(如图),检测情况如下:
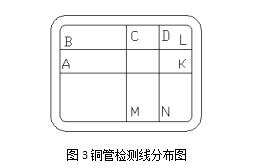
2.1. 实际检测铜管宽面内腔尺寸的变化
2.1.1. 铜管宽面(AK、BL)
对370*480铜管的宽面中心内部尺寸(AK部位),每间隔一定距离各点标注,同时在无水压、水压0.6MPa、水压1.0MPa分别进行检测,检测结果见下表:
表2:不同压力条件下,铜管宽面中心线位置(AK)内腔尺寸的变化
与上口的距离(mm) | 铜管承受冷却水的压力,铜管内腔间距(mm) | 相同位置不同压力下的变化值(mm) | ||||
0MPa | 0.6MPa | 1.0MPa | 无压-0.6MPa | 无压-1.0MPa | 0.6-1.0MPa | |
5 | 383.24 | 382.85 | 382.77 | 0.39 | 0.47 | 0.08 |
100 | 381.85 | 381.39 | 381.05 | 0.46 | 0.8 | 0.34 |
200 | 381.04 | 380.48 | 379.85 | 0.56 | 1.19 | 0.63 |
300 | 380.87 | 379.75 | 379.11 | 1.12 | 1.76 | 0.64 |
400 | 380.05 | 379.44 | 378.72 | 0.61 | 1.33 | 0.72 |
500 | 379.56 | 378.98 | 378.34 | 0.58 | 1.22 | 0.64 |
600 | 379.13 | 378.74 | 378.17 | 0.39 | 0.96 | 0.57 |
700 | 379.05 | 378.62 | 378.17 | 0.43 | 0.88 | 0.45 |
795 | 379.08 | 378.84 | 378.48 | 0.24 | 0.6 | 0.36 |
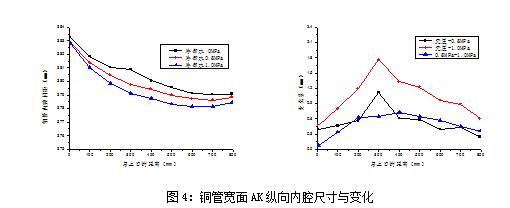
从上图可以看出: AK纵向监测线,随着冷却水压力的变化,相同两个点间距发生微量变形。从无压力到0.6MPa,变形最大值为1.12mm;到1.0MPa,变形最大值为1.76mm;冷却水压力0.6MPa提高到1.0MPa,铜管的变形量最大达到0.72mm。变形的最大点在铜管中部,上下距法兰较近处变形较小。
对370*480铜管的宽面BL位置检测,如下图所示:
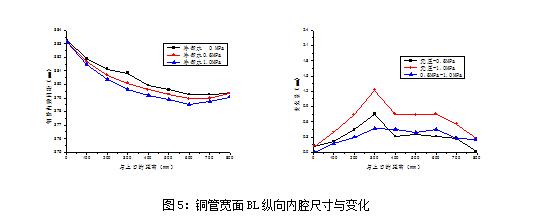
经测量: BL纵向监测线,随着冷却水压力从无压力到0.6MPa,变形最大值为0.75mm;到1.0MPa,变形最大值为1.22mm;冷却水压力0.6MPa提高到1.0MPa,铜管的变形量最大达到0.47mm。变化趋势与AK检测线相同,变形量相对减小。
由于铜管为非理想的梁式结构,理论与实际变形量会有一定的差距,具体如下表:
表3:铜管理论挠度与实测值
名称 | 冷却水压力MPa | 宽面长度m | 铜管壁厚mm | 理论单侧最大挠度(mm) | 检测点 | 两侧最大变形量(mm) | 单侧最大变形值(mm) | 实测/理论(%) |
1 | 0.6 | 0.492 | 32 | 1.3097 | AK | 1.12 | 0.56 | 42.76 |
BL | 0.75 | 0.375 | 28.63 | |||||
2 | 1.0 | 2.1828 | AK | 1.76 | 0.88 | 40.32 | ||
BL | 1.22 | 0.66 | 30.24 |
在370*480铜管宽面的中心(AK),不同压力条件下,实测变形量为理论变形量约40%。在370*480铜管宽面的1/4处(BL),由于距离边部较近,受到两侧的约束,实测变形量为理论变形量约29%。
2.1.2. 铜管窄面中心(CM、DN)
对370*480铜管的窄面中心内部尺寸,每间隔一定距离各点标注,同时在无水压、水压0.6MPa、水压1.0MPa分别进行检测,检测结果见下表:
表4:不同压力条件下,铜管窄面中心线位置(CM)内腔尺寸的变化
与上口的距离(mm) | 铜管承受不同冷却水压力,铜管内腔间距(mm) | 相同位置不同压力下的变化值(mm) | ||||
0MPa | 0.6MPa | 1.0MPa | 无压-0.6MPa | 无压-1.0MPa | 0.6-1.0MPa | |
5 | 495.52 | 495.39 | 495.32 | 0.13 | 0.2 | 0.07 |
100 | 494.17 | 494.09 | 494.01 | 0.08 | 0.16 | 0.08 |
200 | 493.2 | 493.07 | 493.24 | 0.13 | -0.04 | -0.17 |
300 | 492.71 | 492.9 | 492.9 | -0.19 | -0.19 | 0 |
400 | 491.84 | 491.86 | 491.92 | -0.02 | -0.08 | -0.06 |
500 | 491.24 | 491.39 | 491.42 | -0.15 | -0.18 | -0.03 |
600 | 490.75 | 490.74 | 490.76 | 0.01 | -0.01 | -0.02 |
700 | 490.39 | 490.32 | 490.3 | 0.07 | 0.09 | 0.02 |
795 | 490.31 | 490.3 | 490.23 | 0.01 | 0.08 | 0.07 |
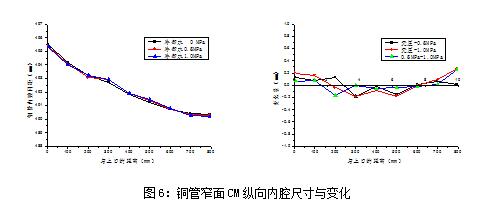
从上图可以看出:CM纵向监测线,从无压力到0.6MPa,变形最大值为0.19mm;到1.0MPa,变形最大值为0.19mm。不过此次变形与宽面中心有所不同,在铜管中心部位相同两个固定点,产生铜管间距加大。且冷却水压力0.6MPa提高到1.0MPa,也出现这种变化趋势。
对370*480铜管的宽面DN位置检测,如下图所示:
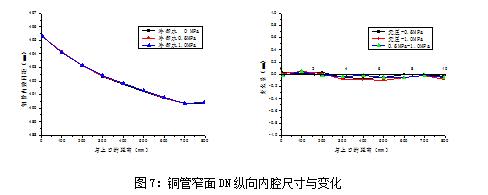
经测量分析:DN纵向监测线,从无压力到0.6MPa,变形最大值为0.07mm;到1.0MPa,变形最大值为0.09mm,与CM检测线变化趋势相同。
在保证铜管冷却水流速(冷却水流量)的情况下,经过现场多次试验,由于铜管冷却过程水压的作用,铜管内壁会发生微量的变形,其检测点的变形量如下表:
表5:0.6MPa-1.0MPa铜管间距变化(mm)
与上口的距离(mm) | 5 | 100 | 200 | 300 | 400 | 500 | 600 | 700 | 795 | |
不同位置处的变化值(mm) | 宽面1/4处(BL) | 0.00 | 0.18 | 0.3 | 0.47 | 0.44 | 0.39 | 0.44 | 0.27 | 0.26 |
窄面1/4处(DN) | -0.02 | 0.04 | -0.02 | -0.03 | -0.02 | -0.05 | -0.06 | -0.02 | -0.05 | |
宽面中心(AK) | 0.08 | 0.34 | 0.63 | 0.64 | 0.7 | 0.64 | 0.57 | 0.45 | 0.36 | |
窄面中心(CM) | 0.07 | 0.08 | -0.17 | 0.00 | -0.06 | -0.03 | -0.02 | 0.02 | 0.07 |
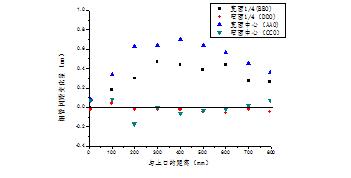
图8:0.6MPa-1.0MPa铜管检测点间距变化图
从上图可以看出:铜管内的水压从0.6MPa,增加到1.0MPa,由于水压力的作用,使铜管沿轴向、径向均发生微量变化,在铜管宽面的中心部位(AK)向内鼓胀的最为严重,随着沿边部的延伸,逐步减小。宽面中心最大的鼓胀值达到0.70mm。在铜管窄面的中心部位(CM)向外鼓胀的最为严重,在上下部位则向内鼓胀,随着沿边部的延伸,逐步减小。这是由于窄面的变形受到宽面变形的影响,在宽面向内发生鼓胀较大时,窄面则向外发生鼓胀。
3. 结晶器承压后铜管锥度的变化
由于窄面的在承受压力时,变形值较小,故仅对宽面的锥度进行研究。
3.1. 本次检测的锥度变化
铜管冷却水压力的变化,造成铜管微量的变形,对连铸坯的断面尺寸影响很小,但对铜管锥度的变化影响较大。对铜管宽面1/2处(AK)、1/4处(BL),同一条线上每间隔一定距离上下两个数值差如下:
表6:铜管承受不同冷却水压力,铜管锥度的变化(mm)
锥度的位置(mm) | 宽面½(AK)锥度 | 宽面¼(BL)锥度 | ||||
无压力 | 0.6MPa | 1.0MPa | 无压力 | 0.6MPa | 1.0MPa | |
5-100 | 0.695 | 0.73 | 0.86 | 0.675 | 0.72 | 0.81 |
100-200 | 0.405 | 0.455 | 0.6 | 0.385 | 0.5 | 0.56 |
200-300 | 0.085 | 0.365 | 0.37 | 0.15 | 0.305 | 0.39 |
300-400 | 0.46 | 0.195 | 0.225 | 0.45 | 0.23 | 0.215 |
400-500 | 0.195 | 0.19 | 0.16 | 0.16 | 0.18 | 0.155 |
500-600 | 0.215 | 0.12 | 0.085 | 0.175 | 0.155 | 0.18 |
600-700 | 0.04 | 0.06 | 0 | -0.005 | -0.02 | -0.105 |
700-795 | -0.015 | -0.11 | -0.155 | -0.04 | -0.175 | -0.18 |
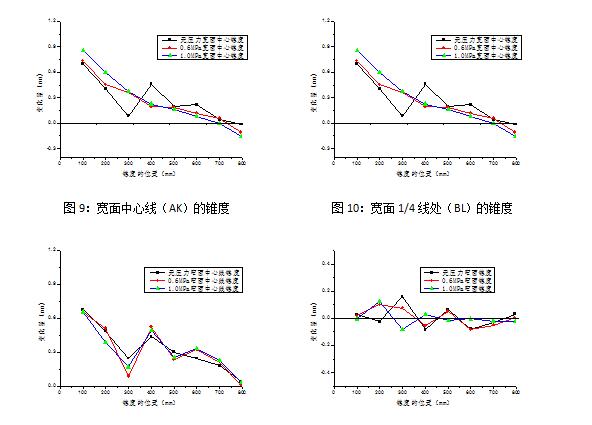
图11:窄面中心线(CM)的锥度 图12:窄面1/4线(DN)的锥度
从上图可以看出:原铜管的锥度在0.6MPa、1.0MPa的冷却水压力下,发生变形,在宽面其拐点也发生明显的变化,窄面锥度也发生一定的变化。
针对这一变化,铜管的原设计的锥度曲线,在冷却水的压力作用下,也应发生相应的变化。假设铜管变形为线性,在中部达到最大值,向上下部逐步线性降低,在上下法兰密封处铜管不变形。则在不同的压力条件下,均匀变形量如下:
铜管宽面中心线,在0.6MPa压力条件下(最大变形量为1.12mm):
0~400mm增加值逐步增加:1.12/400*10=0.028mm/cm
400~800mm增加值逐步降低:1.12/400*10=0.028mm/cm
同样可以计算出在其他状况下,铜管的变化,如下表:
表7:内腔的尺寸理想变化值(mm/cm)
不同水压 | 铸坯宽面中心(1/2) | 铸坯宽面1/4处 |
0.6MPa | 0.028 | 0.01875 |
1.0MPa | 0.044 | 0.0305 |
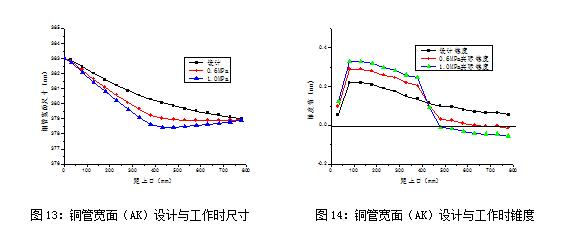
从上图表可以看出:在铜管的宽面AK检测线,原设计铜管的内腔尺寸,在生产过程中(结晶器的冷却水压力达到0.6MPa、1.0MPa),发生了变化,进而影响到铜管的锥度变化,在下半部发生负锥度的情况。由于铜管的变形在最大值在高度方向上的中间,故在铜管的上半部,起到增加锥度的作用,而在下半部减小锥度的作用,甚至出现负锥度的情况。
4. 数值模拟
对铜管(370*480断面,32mm厚度),在不同水压状态,与浇注状态进行数值模拟,模拟结果如下:
表8:结晶器材料及冷却水的热性能
材料 | 导热率(25 ℃~350 ℃) | 比热容J/(kg·℃) | 密度kg/m3 | |
W/(m·℃) | ||||
铜 | 25 ℃ | 335 | 410 | 894 |
120 ℃ | 315 | |||
350 ℃ | 310 | |||
镍 | 82.9 | 460.6 | 8910 | |
钢 | 49 | 460 | 7860 | |
水 | 0.597 | 4187 | 998 |
表9:结晶器各种材料的热性能
符号 T、E、a、sy和 E1 分别代表温度、模量、热膨胀系数、初始屈服强度和线性硬化斜率。材料 | T /℃ | a /℃-1 | T /℃ | E /GPa | sy /MPa | El /GPa |
铜 | 15 | 15.2 X 10-6 | 20 | 128 | 330 | 11 |
71 | 15.7 X 10-6 | 200 | 128 | 280 | 11 | |
127 | 16.5 X 10-6 | 350 | 128 | 240 | 11 | |
227 | 17.6 X 10-6 | 500 | 128 | 165 | 11 | |
327 | 18.3 X 10-6 | |||||
钢 | 20~200 | 11.7 X 10-6 | 20~200 | 200 | ||
镍 | 20~200 | 16.7 X 10-6 | 20~400 | 230 | 700 | 73 |
铜的泊松比,为0.326
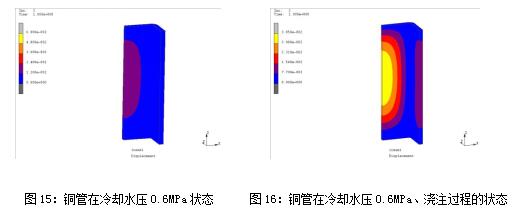
上图为铜管1/4的模拟结果图,从上图可以看出铜管在不同过程的变形状态。
经过数值模拟分析:随着铜管壁厚的变化,在承压状态下,其变形值不同,以370*480铜管为例,得出变形量如下表:
表10:不同壁厚铜管的理想最大变形量
名称 | 冷却水压力MPa | 宽面长度m | 铜管壁厚mm | 宽面AK检测线实际最大变形值(mm) | 宽面DN检测线实际最大变形值(mm) |
1 | 0.6 | 0.492 | 32 | 0.524 | 0.380 |
2 | 0.8 | 0.699 | 0.506 | ||
3 | 1.0 | 0.873 | 0.633 | ||
4 | 0.6 | 0.492 | 30 | 0.636 | 0.461 |
5 | 0.8 | 0.848 | 0.615 | ||
6 | 1.0 | 1.060 | 0.768 | ||
7 | 0.6 | 0.492 | 28 | 0.782 | 0.567 |
8 | 0.8 | 1.043 | 0.756 | ||
9 | 1.0 | 1.303 | 0.945 |
5. 结论
5.1. 在承受不同冷却水压的状态下,铜管的形状对变形量、锥度有一定的影响。
5.2. 经过测量与分析,在工作压力的状态下,矩形铜管宽面大于窄面变形量,中部大于两侧变形量。
5.3. 减薄铜管壁,受冷却水压、浇注过程的热变形的影响较大。
参考文献:
[1] 蔡开科.连铸结晶器[M].北京:冶金工业出版社, 2008.