板坯鼓肚及凹陷的原因分析及控制
来源:2019全国高效连铸应用技术及铸坯质量控制研讨会论文集|浏览:次|评论:0条 [收藏] [评论]
板坯鼓肚及凹陷的原因分析及控制朱振毅,张永亮,王克忠(山东泰山钢铁集团有限公司热轧部)摘要:介绍了连铸板坯形状控制在板坯连铸生产过程中的重要意义,造成连铸板坯鼓肚及凹陷缺陷的原因…
板坯鼓肚及凹陷的原因分析及控制
朱振毅,张永亮,王克忠
(山东泰山钢铁集团有限公司热轧部)
朱振毅,张永亮,王克忠
(山东泰山钢铁集团有限公司热轧部)
摘要:介绍了连铸板坯形状控制在板坯连铸生产过程中的重要意义,造成连铸板坯鼓肚及凹陷缺陷的原因以及采取的相应措施。
关键词:板坯;鼓肚;凹陷;缺陷;措施。
1前言
在板坯连铸生产过程中,板坯形状控制的意义,不仅仅是控制坯形符合客户和下游工序标准质量要求,更重要的是通过控制坯形来有效控制生产事故及产品质量。泰钢炼钢厂有两台150mm×(770-850mm)两机两流直弧形板坯连铸机,分别是2003年和2006年投产使用,在生产实践中,通过研究板坯鼓肚及凹陷的产生原因,制定了相关的控制措施,解决了现场实际生产中的若干问题。
2铸坯鼓肚
2.1概念及危害
鼓肚是指铸坯坯壳受到钢水静压力的作用而鼓胀成凸面的现象,板坯表面中心凸起最大值与边缘的厚度差叫鼓肚量,以此来描述铸坯鼓肚变形程度,在板坯发生的鼓肚分为宽面鼓肚和窄面鼓肚,宽面鼓肚发生在铸坯内外弧,宽面鼓肚会引起液相穴内富集溶质钢水产生流动,引起严重的中心偏析和中心裂纹,严重宽面鼓肚会使板坯拉不出来,造成停机事故(图1);窄面鼓肚是一种常见的铸坯缺陷,正常铸坯窄面应该是向内微凹,窄面鼓肚往往伴随着偏离角凹陷,板坯凹陷部位伴随着皮下裂纹或结疤,皮下裂纹是漏钢的前兆,板坯无法修磨并且很难轧合。
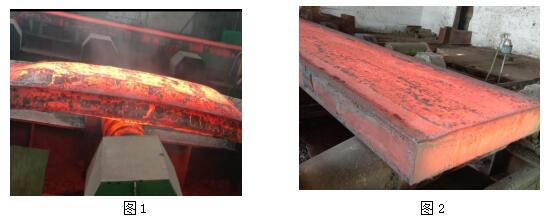
2.2鼓肚原因
2.2.1钢水过热度、拉速、二次冷却影响在钢水过热度高、拉速快、冷却不良的情况下,使铸坯温度过高,坯壳薄、坯壳强度低,在钢水静压力作用下容易造成坯売鼓肚。板坯拉速过高、二次冷却过弱,使铸坯液芯长度超过铸机的治金长度,拉出铸机后会形成宽面鼓肚。拉速变化的影响:尤其是前一炉温度高、拉速慢,浇注炉次拉速过快,拉速变化幅度过大,相应二冷水量未能跟随增加,造成铸坯回温液芯延长而缺少有效夹辊支撑,受到整个铸机高度的液态钢水静压力作用造成铸坯出扇形段的铸坯宽面鼓肚。
2.2.2扇形段开口度影响
扇形段辊子开口度变大,不利于铸坯凝固末端的压合,液态钢水在静压力作用下继续填充凝固末端空隙,高温坯壳强度低、塑性变形能力较好,容易产生鼓肚。
2.2.3结晶器锥度的影响
结晶器锥度过小或结晶器下口磨损严重,铸坯过早脱落结晶器壁,为导致板坯窄面鼓肚的原因之一。不同的钢种具有不同的收缩率,结晶器锥度调整应与钢种相对应,锥度过大容易粘结漏钢,锥度过小则容易产生侧面鼓肚。
2.2.4足辊的影响
坯壳刚出结晶器时比较薄,如側面足辊支撑不足,则容易产生侧弧鼓肚。应该将足辊“硬”一些,即将足辊面调进结晶器侧弧线以内0.5mm左右,使坯売收到轻微挤压,不会产生侧弧鼓肚。
2.2.5扇形段设备方面
扇形段液压系统故障造成的失压、扇形段抬起、扇形段夹辊断裂、夹辊弯曲变形等问题,可导致较严重的鼓肚现象。
2.3预防及控制措施
2.3.1根据生产钢种特性,调整合适的结晶器锥度,及结晶器足辊的弧线位置,理论计算与生产实践相结合,制定工艺参数。
2.3.2制定合理的温度、拉速控制制度。实际生产中严格控制钢水过热度(一般在10~25℃),稳定铸坯拉速,避免前后炉次拉速波动过大,如拉速变化大,特别是由慢变快时,二次冷却水量也应同步增加,避免出扇形段鼓肚。
2.3.3制定合理二冷配水制度,板坯铸机应使用动态二冷配水制度。
2.3.4制定合适的扇形段开口度。加强扇形段开口度的监测、调整。做好扇形段辊子弯曲情况监测,发现问题及时更换,可采用多节辊防止辊子变形,做好扇形段液压系统的维护、点检,防止液压失压或扇形段抬起,提高扇形段夹辊质量并做好日常点检,防止夹辊断裂。
3板坯凹陷
3.1概念及危害
板坯凹陷部位表面凹下最大值与边缘的厚度差叫凹陷量,板坯凹陷主要有宽面凹陷和窄面凹陷,宽面凹陷多发生在板坯角部附近,由于凹陷部位冷却和凝固速度比其它部位慢,组织粗化,裂纹敏感性强,在热应力和钢水静压力作用下,凹陷薄弱处产生应力集中而出现裂纹,铸坯表面凹陷越深,坯壳厚度不均匀性就越严重,裂纹出现的几率越大,严重时会发生漏钢。铸坯窄面出现微凹是正常现象如果坯壳受到挤压,则窄面只能往里收,而不能往外鼓,结晶器的锥度过大和过小,都会造成窄面凹陷发生。还有一种纵向凹陷产生原因为铸坯在高温下受到柔性挤压所致,零段辊子不转,保护渣、氧化铁皮填充到不转的扇形段辊子及铸坯表面之间,由于此时铸坯表面温度高,抗压强度低,导致此类凹陷的产生(图2),且随着浇次的进行不断发展,通过加强对扇形段的检查、维护、改善润滑,此类凹陷就会消除。
3.2凹陷原因
3.2.1宽面凹陷:其产生原因为铸坯在扇形段内产生较严重的鼓肚,鼓肚后铸坯经过下一扇形段或下一夹辊后,面部鼓肚部位受到夹辊向铸坯内部压力被逐渐压平,但由于窄面及角部坯壳较厚、偏离角部坯壳薄,造成偏离角部坯壳向铸坯内部陷入,形成了偏离角部的严重凹陷,凹陷部位内部受到张力作用,伴随凹陷产生角部内裂这种严重缺陷的产生原因主要为:在坯壳凝固末端以上某一扇形段液压系统故障失压造成的扇形段抬起、扇形段夹辊断裂或扇形段夹辊弯曲严重。
3.2.2钢水成分影响。碳含量在0.10%~0.15%的钢种在凝固过程中发生包晶反应,伴随着较大的线收缩,产生的气隙使各部分传热不均匀,造成局部冷却不足产生凹陷,尤其在偏离角部位,坯壳最薄,凹陷及角部内裂纹易在此处产生,严重时造成角裂漏钢,这就是普碳钢易发生偏离角凹陷及角部结疤裂纹的主要原因。
3.2.3结晶器方面的影响。结晶器铜板或铜管磨损严重或镀层剥落时,组合式结晶器铜板厚度不均匀,结晶器四周水缝不均匀或水缝堵塞等原因,造成铸坯在结晶器内冷却不均匀,使得出结晶器坯壳厚度不均匀,坯壳较薄的部位受到强烈的二冷喷淋冷却,凝固收缩力不均匀易发生凹陷;另外结晶器冷却强度过大造成角部收缩明显,促进气隙形成,增加传热阻力,而造成凹陷。
3.2.4保护渣影响。结晶器保护渣传热性能不良关键影响因素为保护渣黏度,保护渣黏度过低时,则易造成传热的不均匀性,从而产生铸坯凹陷。
3.2.5扇形零段影响。如结晶器与扇形零段对弧偏差较大,造成坯壳偏离结晶器铜板而出现坯壳与铜板间的传热不均匀,因角部坯売较厚不易变形,而大面坯売因钢水静压力作用贴于铜板,产生轻微鼓肚,在进入零段后,在偏离角部产生凹陷;另外零段夹辊弯曲严重时,铸坯产生间隙鼓肚,易造成偏离角凹陷。
3.2.6振动影响。振动不平稳,振动南北偏摆量过大,造成液面不稳定、坯壳受到不均匀力作用,常导致连续凹陷的产生。
3.2.7温度、拉速影响。钢水温度过高或拉速过快,都将导致在结晶器内生成的坯壳薄,坯壳不均匀性严重,承受应力的能力减弱,坯売薄弱处易产生凹陷、内裂。
3.2.8水口对中。水口对中不良,易造成结晶器内坯売厚度的不均匀,出现局部应力集中而产生凹陷及偏离角内裂。
3.3控制措施
3.3.1一般轻微的窄面整体圆弧状凹陷属正常现象,对铸坯凹陷量的要求则对轧制方面影响不大,其形成的主要原因为足辊调整偏“硬”导致。
3.3.2为预防大面偏离角的严重凹陷,应做好扇形段液压系统的维护、点检,防止液压失压或扇形段抬起,提高扇形段夹辊质量并做好日常点检,防止夹辊断裂,偏离角部位出现严重凹陷后应立即停机,避免损失过大,停机后处理液压系统故障或更换扇形段。
3.3.3尽量控制钢中碳含量避开包晶反应区,[C]向上限或下限控制。
3.3.4安装时保证结晶器水缝均匀,提高结晶器材质,防止结晶器磨损严重及镀层脱落,结晶器实施弱冷冷却,合理控制冷却强度。
3.3.5根据钢种特性选用合适的保护渣,适当提高结晶器保护渣黏度,提高保护渣传热均匀性,保护渣加入时坚持勤加少加原则。
3.3.6提高扇形段对弧精度,尤其是结晶器和零段,发现零段夹棍弯曲变形严重及时进行更换。
3.3.7检测振动台平稳性,保证振动台南北偏摆≤0.2mm,东西偏摆≤0.15mm。
3.3.8适当增加窄面足辊与铸坯的接触程度,防止铸坯鼓肚,但足辊不应调整过硬,否则可能会造成拉坯阻力大,侧面铸坯凹陷过大。
3.3.9控制好钢水过热度,确定合适的拉速制度,防止温度过高、拉速过快造成的坯壳过薄。
3.3.10严格水口装配,保证水口对中良好,防止偏流保证铸坯均匀冷却凝固。
4结论
板坯出现形状缺陷主要原因是由设备问题引起的,从工艺上可以采取措施进行弥补,反过来,也可以通过形状缺陷判断设备存在的问题,进行有针对性的检修,避免出现生产、质量事故。