河钢承钢方坯连铸机提速及提温生产实践
来源:2019全国高效连铸应用技术及铸坯质量控制研讨会论文集|浏览:次|评论:0条 [收藏] [评论]
河钢承钢方坯连铸机提速及提温生产实践尹英波,李剑华,温日春,杨建永,潘爱龙,陈英奇(河钢集团 承钢分公司 线材事业部 河北 承德)摘要:本文介绍了通过对河钢承钢股份有限公司线材事…
河钢承钢方坯连铸机提速及提温生产实践
尹英波,李剑华,温日春,杨建永,潘爱龙,陈英奇
(河钢集团 承钢分公司 线材事业部 河北 承德)
摘要:本文介绍了通过对河钢承钢股份有限公司线材事业部1#方坯连铸机结晶器足辊区冷却及支撑装置改造、振动机构调试优化、二冷段喷淋系统改造、 矫直区不必要的二次冷却优化、工艺过程控制优化,实现铸机提速2.4-2.6m/min的生产及铸坯温度提升10-22℃,方坯提速及提温达产达效节能生产的目的。
关键词:铸机;改造;优化;提速;提温
Abstract: This paper introduces the secondary cooling optimization and process control of the second cooling and straightening zone through the cooling and supporting device transformation of the roller zone of mould, the adjustment and optimization of vibration mechanism, the modification of the spray system in the second cooling section and the straightening area of the continuous casting machine of the wire division of Hesteel Chengsteel. The purpose of achieving the speed increase of the casting machine 2.4-2 .6 m/min and the temperature increase of the casting billet by 10-22 °C, the speed increase of the billet and the effective energy saving production of the production.
Production practice of speed-up and temperature -up of billet caster in chengde iron and steel Co.,Ltd
Yin Yingbo,Li Jianhua,Wen Richun,Yang Jianyong,pan Ailong,Chen Yingqi
(Hbis Group Chenggang Branch Wire rod Business Division Hebei Chengde)
Key words: Casting;Transform;Speed Up;Optimize;Tiwin
1 前言
2 重点改造项目及特点
1 前言
在我国,高效连铸技术的研究很早就已起步,在固定式结晶器及一般钢种条件下, 连铸机的浇铸速度还有很大潜力, 可大幅提高。连铸生产中的设备维护管理、工艺操作制度的严格执行、科学的生产调度是高效连铸技术的基础。钢厂在实现铸机高效化过程中的作用是最大的和最关键的。河钢承钢线材事业部,R7m 六机六流直轧小方坯连铸机(165×165mm)自2017年10月投产后3个月即达到了设计的各项指标,2018年年产量达到了106万吨。单机全连铸生产要求钢产量稳定,要求铸机提高拉坯速度,保证充足的设备检修优化时间。随着炼钢能力的不断增加,铸机基础作业率达到了85%以上,铸机原设计已不能满足生产的特定要求,因此河钢承钢进行了高效化整改改造,经过一年多的生产实践证明,效果显著。
2 重点改造项目及特点
此次铸机改造的主要目的是提高铸坯拉速和提高铸坯表面温度。制约铸坯拉速和铸坯表面温度因素很多,但对于铸机本体讲,关键在于结晶器足辊区良好的稳定冷却及支撑、振动系统的稳定运行、二冷段均匀分布冷却及避免矫直区不必要的二次冷却干扰,以及工艺过程控制是重要因素。
2.1 结晶器足辊区冷却及支撑装置改造
结晶器是连铸机的关键部件,也是制约铸机高效生产的最为关键的环节。高效方坯连铸对结晶器的要求就是要在高拉速的条件下,钢水能够在结晶器内均匀形壳,并在结晶器出口位置达到一定的坯壳厚度。采用了“新型单体环形双排水环”如图1 进行铸坯出结晶器下口的冷却支撑,避免了因冷却不均造成的角裂漏钢及形变。新增加四个足辊 如图2,足辊本体采用铜套石墨轴心组装,确保铜管倒锥度与钢种及拉速相匹配,在线结晶器铜管镀层完好,铜管内腔倒锥度光滑过渡且正方度保持较好。有效克服了因支撑不足,冷却强度不到位,制约拉坯速度的提升。
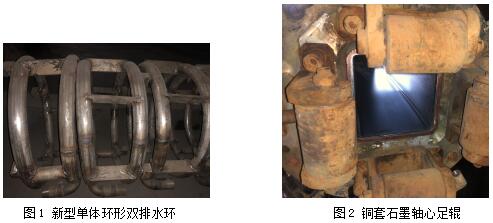
2.2 振动机构调试优化
铸机原振动为两偏心单连杆式振动系统,此振动装置的缺点是振动过程中仿弧精度差,高拉速状态下,结晶器稳定性不好出现偏摆,很难适应高拉速的要求。为此采用了四二式单板簧振动系统,有效克服了高拉速状态下结晶器偏摆现象。结晶器偏摆由原0.32-0.40mm/m控制降低在0.20-0.26mm/m,结晶器纵向偏摆稳定降低了0.2mm/m,控制在0.22-0.28mm/m。通过对振动机构调试优化,有效地提高了两偏心单连杆式振动系统的稳定运行。为铸坯提速奠定了坚实基础。
2.3 二冷段喷淋系统改造
优化喷淋集管布置,改进二冷制度,采用“新型单流单体独立水条内悬挂技术”见图1 ,均匀分布冷却区间,六机六流12个冷却小区间冷却由强到弱,阶梯式递减,铸坯冷却喷距精度差控制到了0.3-0.5mm之间。同时在保证切割时铸坯芯部全凝固条件下,尽可能减小冷却强度,更好地利用凝固潜热,提高铸坯温度,见图2。 通过实测的方法得到目前各冷却回路的最大水量,重新进行喷嘴选型如表1,改造增加一段水条,将水条全部改造成统一标准,分三个区域控制,采用全水冷却防止。优化配水二次方程,比水量控制1.15l/g,满足高拉速的水量要求,保证铸坯质量。通过二冷段喷淋系统改造解决了喷距精度不够问题,解决了冷却不均及冷却临界点控制问题。
表1.水嘴选型
型号 | 个数 | 压力 | |
一区 | 3/8”PZ11167QZ5 | 5 | 0.7Mpa |
二区 | 1/4”PZ7065QZ5 | 10 | 0.7Mpa |
三区 | 1/4”PZ7065QZ5 | 9 | 0.7Mpa |
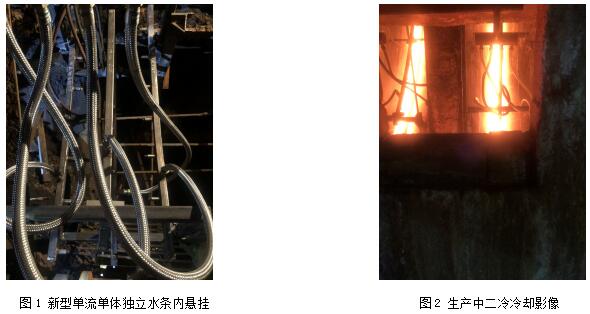
2.4 矫直区不必要的二次冷却优化
拉矫装置维持现有结构形式不变,对拉矫机1号辊区、2号辊区、分离辊区设备冷却水进行管路改造,将外冷却水管改为内循环冷却管路,对各流单体拉矫装置安装“新型卡嵌式水冷罩”,保证冷却设备运行的同时,防止设备冷却水喷溅到铸坯表面,造成铸坯温度降低。通过对矫直区优化解决了跑水漏水对铸坯进行二次冷却温降。
2.5 工艺过程控制优化
随着过热度的升高,铸坯中心疏松、缩孔和偏析级别都会大幅度提高,即中包温度对铸坯质量有重要影响,甚至导致铸坯不合格。因此连铸机提高拉速必须确保出钢周期、钢水温度和成份相对稳定。钢水精炼、调温:采用精炼、调温,均匀化学成份,均匀钢水温度,稳定过热度,降低非金属夹杂物。
2.5.1 钢水质量条件控制
杂质元素的控制,为降低铸坯裂纹敏感性、减少夹杂物富集,从而提高连铸生产的可操作性、改善铸坯质量,各钢厂对钢水中有害杂质元素含量要求均比国家有关标准严格,主要成分指标:[P] ≤0.035%,[S] ≤0.025% ,Mn/S ≥25。
2.5.2温度制度优化
钢水过热度是影响连铸操作的重要因素,控制不好将直接导致铸坯质量问题,甚至造成拉漏事故,通常中间罐内钢水过热度控制为15-40℃。每包钢水的浇注初期和末期应根据中间罐内钢水过热度的变化来调整拉坯速度,确保铸机生产中的热态平衡,最高/最低温度差应严格控制到35℃,避免中包内钢水温度的过度波动。除提供温度均匀的钢水、控制钢水浇注时间以外,需对钢包及中间罐内的钢水进行保温,减少温度损失,主要措施有:
(1)对中间罐内衬进行充分预热,预热温度大于1000℃,时间大于60min。采用新式“热值区间烘烤技术,保证预热烘烤温度的同时,强化了中间罐内衬二次凝固强度及内腔环境温度。
(2)采用钢包液压加盖装置及中间罐二次密封技术,稳定钢温状态的同时避免钢液二次氧化,净化钢液夹杂,从而提高钢液可浇注质量。
(3)钢包、中间罐钢水液面采用保温隔热覆盖剂,这是一项最直接有效的钢液隔热保温防氧化去除杂质环节。
2.5.3 炉机匹配制度控制
正常生产开始浇注,采取“头炉小二炉大”的衔接式浇注提速匹配方式,达到转炉与连铸工序之间时间节奏协调,两者生产节奏稳定提升的同时,为铸坯温度提升控制提供了量化空间,实现双得即:拉坯速度提升及铸坯温度提升。
方坯铸机的拉速控制由1.8-2.0m/min提高到了2.4-2.6m/min在此分别制定了HRB500E,HRB400E温度、拉速细节控制制度,生产流数由八流减为六流,实现轧机、连铸、转炉整体生产节奏匹配。
通过对工艺过程控制优化解决了制约铸机提速、提温等因素,为后期达产达效创造有利条件。
3 改造效果
提速铸机改造于2017年10月完成,进行“提高拉速”生产工艺改进并组织生产试验,2018年产钢达到了106万吨。铸机使用∮16.5mm快换短滑块开浇。开浇头坯过拉矫机在铸机设备及各工艺参数运行稳定,中间包温度符合要求的情况下组织换水口之前手动提高冷却水流量:足辊10-11m3/h,一区15-18m3/h,二区10-11m3/h,二冷水稳定后组织6个流全部更换∮18.5-19mm快换滑块,转为自动配水强冷。使用∮18-19 mm快换滑块满包敞开浇注,拉速2.4-2.6m/min之间,及时调整中间包液面,确保拉速控制在了2.5m/min,浇注周期40分钟。试验控制工艺参数情况如表2。
①改造后,提速前正常拉速控制在1.8-2.0m/min,提速后正常拉速稳定在2.4-2.6m/min,可比原来铸坯拉速提高0.6m/min,铸坯质量符合轧制要求,提速后保证了连浇炉数提高到现在的50炉/浇次。铸机作业率显著提高,真正实现了达产达效。
表2.铸生产工艺参数
炉次号 | 18***01 | 18***02 | 18***03 | 18***04 | 18***05 | 均值 | |
中包温度 | ℃ | 1543 | 1546 | 1547 | 1540 | 1528 | 1544.4 |
拉速 | m/min | 2.53 | 2.45 | 2.43 | 2.47 | 2.7 | 2.5 |
足辊水 | m3/h | 9.52 | 10.48 | 10.09 | 10.33 | 11.40 | 10.36 |
一区水 | m3/h | 13.14 | 13.47 | 13.40 | 14.24 | 15.20 | 13.89 |
一区水 | m3/h | 9.23 | 9.44 | 9.44 | 9.88 | 10.80 | 9.76 |
比水量 | l/g | 0.99 | 1.15 | 1.08 | 1.11 | 1.23 | 1.11 |
测量矫直温度 | 1073 | 1112 | 1124 | 1163 | 1145 | 1123 | |
切割点表面温度 | 980 | 1007 | 1032 | 1055 | 1040 | 1023 | |
铸坯切 后温度 |
头部 | 938.8 | 969.7 | 943.2 | 997.6 | 1007 | 971 |
尾部 | 995 | 1025 | 991 | 1019 | 1000 | 1006 | |
头尾温差 | 56.9 | 55.3 | 47.8 | 21.4 | 40 | 44 |
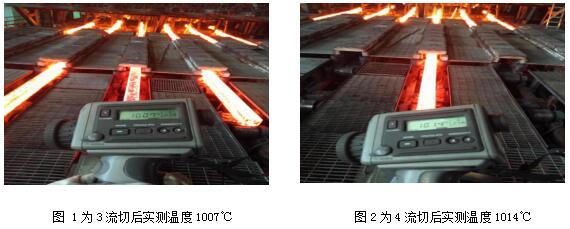
②改造后,通过对现场实验数据跟踪,测量铸坯温度平均值:头部938.8-1007℃之间,切割点温度995-1019℃之间,头尾温差平均控制在44.2℃。同比改造前提高了10-22℃,铸坯温度的提升对直轧产线顺产轧制起到了关键性的作用。通过2018-2019年中旬生产证明各项技术指标较改造前都有较大提高。
4 结语
河钢承钢1#方坯连铸机改造后,可比原来铸坯拉速提高0.6m/min左右,铸坯质量符合轧制要求,拉速的提高使连浇炉数提高到现在的50炉/浇次,铸机作业率显著提高。铸坯表面温度同比改造前提高了10-22℃,为直轧产线达产达效奠定了坚实基础。
参考文献:
[1]孙永栋,高龙永.连铸板坯凝固壳厚度的研究和应用.连铸.2011,(5):5
[2]史宸兴主编.实用连铸冶金技术.冶金工业出版社.2003:29-49