潍坊特钢1360m3高炉停炉降料面总结
浏览:次|评论:0条 [收藏] [评论]
潍坊特钢1360m3高炉停炉降料面总结潍坊特钢技术科 王心乾炼铁厂2号高炉(1360m3)于2007年9月份开炉投产至2017年12月份停炉,一代炉龄10年零3个月,期间共生产铁水2377855.13t,单立方产铁…
潍坊特钢1360m3高炉停炉降料面总结
潍坊特钢技术科 王心乾
炼铁厂2号高炉(1360m3)于2007年9月份开炉投产至2017年12月份停炉,一代炉龄10年零3个月,期间共生产铁水2377855.13t,单立方产铁量9101t/m3。炉役后期由于炉衬及炉缸侵蚀严重,炉腹冷却壁损坏较多,炉壳局部发红需外部喷水冷却等诸多原因,已严重威胁高炉的安全生产。公司决定于2017年12月1日空料线停炉大修,更换炉底碳砖和全部冷却壁。本次停炉空料线采用前期煤气回收打水降料面的方法,于2017年12月1日中午11:50送风,开始降料面,12月2日凌晨0:17高炉休风,整个空料线历时11小时30分钟,料面安全降到风口中心线以下。
1、停炉前的准备工作
为实现快速、安全的降料面,炼铁厂成立停炉领导小组,事先制定了详细、周密的操作方案,统一思路后,严格按照停炉方案执行。
1.1高炉操作调整
(1)停炉前2#高炉炉况顺行度较高,铁水产量和指标参数均在较好水平,高炉热风压力380kpa,日产铁水4100吨,平均燃料比500kg/t。综合考虑到2号高炉炉缸活跃程度高,中心与边缘气流分布均匀,炉墙较为干净,为降低消耗损失,就没有采取洗炉措施,只在停炉前一天,把炉温提到0.7—0.8%,适当降低炉渣碱度,用高温气流.均热炉渣象征性清洗炉缸.炉墙,减少了停炉前的炉况波动和燃料消耗,避免洗炉出现炉皮发红甚至烧穿事故,保证停炉的顺利安全性。
(2)停炉料。12月1日夜班4:50开始上停炉料,配比烧结69%+球团8%+PB块23%。停炉料分Q1、Q2两段,Q1停炉料:(原矿批40t/批)矿批28t/批,干焦批:8.91t(包括焦丁0.3t),硅石300kg/批,综合负荷(干):3.14t/t.干焦比530kg/t,理论碱度1.02.Q1停炉料共上20批。Q2停炉料:矿批24.5t/批,干焦批:8.51t(包括焦丁0.3t),硅石450kg/批,综合负荷(干):2.88t/t.干焦比580kg/t,理论碱度1.03.Q2停炉料共上14批,Q1、Q2停炉料共34批。调整上料制度:矿 31/3 28.5/3 26/3 , 焦 34/2 32/2 30/2 28/2 26/2 24/2 16/2,适当发展边缘气流。后紧跟5批盖面焦,盖面吨数:8.6t * 5批= 43t。
(3)预休风。按计划预休风前倒空矿焦仓、矿焦槽,并控制休风时料线4m--5m。12月1日7:20打开西铁场铁口出铁,8:15按停炉计划预休风,安装炉顶打水枪。预休风时雷达探尺显示料线6.6m(提前用机械探尺标定雷达探尺,雷达探尺显示比实际料线浅2m左右)。以下是预休风前铁水及炉渣成分见表1。
潍钢2号高炉预休风前铁水、炉渣成分(%)
表.1
铁次 | [Si] | [s] | [Mn] | (SiO2) | (CaO) | (Al2O3) | (MgO) | R倍 |
54015次 | 0.65 | 0.024 | 0.23 | 31.59 | 36.27 | 16.13 | 10.39 | 1.15 |
54016次 | 0.68 | 0.023 | 0.23 | 30.98 | 37.05 | 15.82 | 10.43 | 1.19 |
1.2 .外围准备工作。
(1)优化炉顶雾化打水装置。高炉提前改进自制炉顶打水枪,打水枪规格:打水枪总长4.2米,在炉内长度(法兰盘前段)约3米,打水枪内管径45mm,从水枪前端开始每隔10mm左右钻4排眼,共钻眼21排,距离炉墙1米范围内没有开孔(保护炉墙)。在打水枪后头(法兰盘后端)1/3处斜45度角再接焊一根(1寸)水管。打水枪使用方法:原直送的45mm管道通氮气,阀门全开保证通入足量氮气,增加水的雾化程度;斜着焊接的水管通高压水,使用时固定氮气量,通过调节水量大小控制顶温。在降料面过程中炉内煤气量骤增,吹入氮气在一定程度上能稀释炉内的氧气和氢气浓度,同时防止高温气流堵塞打水枪孔道。将自制打水枪在停炉前进行进行模拟操作试验,测的最高打水量(90m3/h),以及不同打水流量的雾化效果,提前调试好打水枪,以便空料线作业时可控制好水压和流量,保证最佳雾化效果。下图就是潍钢自己制作的打水枪及实验时的雾化效果图。
图一
图二
(2)为避免停炉过程中冷却设备向炉内大量漏水,高炉提前联系看水工进行查水.检漏,关掉漏水冷却壁。同时对炉体的密封情况进行检查,对所有的漏点做好标记,利用预休风机会进行焊补处理。
(3)提前校正机械探尺和雷达探尺、在线煤气检测系统、校对炉顶上升管四根电偶、炉顶温度表、炉顶压力表,确保温度、压力准确可靠,保证数据的准确性。检查炉顶荒煤气切换系统、热风炉系统及各蒸气、N2阀门,保证开关灵活。
(4)、残铁沟安放到位,平台铺设整齐,烧残铁口用氧气接现场,使用工具准备整齐。炉前根据铺设平台位置,演示氧枪氧管距离、长度,并试压,备足出残铁的铁水包(9个),提前做好准备工作。
2、停炉降料面
2.1. 降料面操作要点
2.1.1.料面位置的确定
停炉降料线期间,根据雷达探尺数值和煤气成份变化及焦炭燃料消耗情况三者相结合,判断料面位置。煤气成份变化规律:开始阶段CO2体积分数不断降低,H2体积分数不断升高,煤气中CO2降到最低水平(CO2 3%~5%),煤气中H2含接近6-8%,说明料面已进入炉腰区。CO体积分数开始降低,CO2体积分数从最低点开始增加时,说明料面已进入炉腹;当N2含量开始上升时,说明料面已进入风口区;当CO2和CO体积分数相同时,表面降料面操作已接近尾声。吨焦风耗以2500m3/min为基准进行校核。
2.1.2停止回收煤气的条件
(1)当料线空到炉腰部位时,出现下列情况时,停止回收煤气。
(2)煤气中CO2降到最低水平(CO2 3%~5%)。
(3)煤气中H2含接近8-12%。
(4)出现爆震时,压差波动超过20Kpa.
(5)煤气温度高,布袋除尘入口温度接近220℃(>10分钟)。
(6)布袋荒净煤气压差达到9kpa。
2号高炉回收煤气成份变化曲线
图三
2.1.3. 顶温控制
停炉过程最关键是顶温的控制。顶温严格控制在250℃-400℃以内,顶温主要通过炉顶打水、降低风温和风量三种手段来控制。打水量过多,炉顶温度过低,水可能直接打在料面上,这极易产生水汽爆震;相反炉顶温度控制过高,易烧坏炉顶设备。本次停炉过程炉顶打水采用了自制改进的雾化打水枪,有效控制了炉顶温度又避免了水汽爆震,顶温控制在250℃-400℃之间,由于雾化水在没有到达料面之前,便已吸热汽化,避免了与高温料面接触,从而避免了水蒸汽因体积急剧膨胀而引起爆震。停炉过程中,由于炉顶打水雾化效果好,风压、顶温一直稳定在合理范围内,波动很小,直至空料线结束。
炉顶打水量变化情况
图四
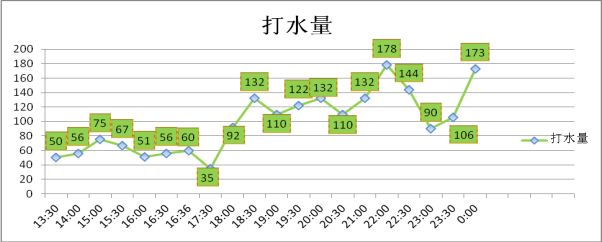
2.1.4.风量、风温的控制
炉内操作上严格控制风量,维持适当的煤气速度,防止产生管道行程,随着料线降低,逐步减少风量。炉腰以上尽量维持正常60%--80%的风量,顶压维持正常80%--90%的水平。当料线到达炉身下部,炉墙粘结物开始塌落,压量关系频繁出现尖峰波动,应及早减风并适当减少打水量,炉腰部位应保持正常60%--70%的风量水平。进入炉腹区域,过了成渣带逐步进入了缓冲区,应保持正常50%--60%左右的风量水平。总体上,前期可保持高炉尽量使用高顶压、大风量、高顶温,可以缩短降料面时间,保证充足的渣铁温度。在保证顶温在合适范围内的前提下,风温可保证较高水平,及时控制风量、打水量,以保证降料面的安全、快速。
2.2. 降料面过程
12月1日12:50高炉预休风后送风,随即引煤气、改高压,13:30风量2612m3/min、风压0.263MPa、顶压0.170MPa、风温1139℃,雷达探尺6.6m.为加快下料速度,缩短停炉时间,将手动打水量控制在50m3/h的较高水平,不动风量、风温,以自动打水控制顶温。随着料面的下降,料层开始逐渐变薄,顶压开始出现波动出现冒尖现象,16:12左右风量减到2050m3/min ,煤气中H2含量在4%左右,Co2含量降低到3%,H2含量高于Co2含量1%,Co含量下降到20%左右。维持半小时左右时间后,观察雷达探尺在14.5mm(预测料面实际位置在炉腰中部),顶压明显波动频繁时,进行切煤气操作,煤气回收结束。在19:22左右3#风口黑,小套底部开始淌水,逐步减风至1500 m3/min 左右,20:50左右4#风口黑,到21:301#、2#、3#、4#、5#风口全黑,底部淌水明显,22:16左右20#、1#、2#、3#、4#、5#、6#风口全黑,此时雷达探尺显示位置17.41米(预测实际位置19.41m),已到达炉腹下沿位置,炉前开始出最后一炉铁(第三炉),出铁过程中,不断将炉顶放散倒替放下,提高炉内压力,力争最大能力出净炉内渣
序号 | 时间 | 风量 | 风压 | 风温 | 打水量 | 雷达探 尺 | 顶温 | ||||
1 | 2 | 3 | 4 | 平均 | |||||||
1 | 13:30 | 2652 | 263 | 1139 | 50 | 6.6 | 246 | 270 | 336 | 311 | 291 |
2 | 14:00 | 2592 | 251 | 1117 | 56 | 8 | 303 | 370 | 266 | 280 | 305 |
3 | 15:00 | 2283 | 243 | 1123 | 75 | 9.9 | 251 | 353 | 224 | 255 | 271 |
4 | 15:30 | 2307 | 234 | 1140 | 67 | 10.5 | 218 | 322 | 198 | 187 | 231 |
5 | 16:00 | 2273 | 227 | 1135 | 51 | 11.92 | 234 | 313 | 211 | 214 | 243 |
6 | 16:30 | 2155 | 201 | 1148 | 56 | 13.74 | 275 | 277 | 268 | 284 | 276 |
7 | 16:36 | 1850 | 145 | 1161 | 60 | 14.6 | 258 | 230 | 281 | 275 | 261 |
8 | 17:30 | 1252 | 46 | 1172 | 35 | 15.37 | 442 | 296 | 305 | 182 | 306 |
9 | 18:00 | 1349 | 50 | 1172 | 92 | 15.51 | 430 | 283 | 307 | 207 | 307 |
10 | 18:30 | 1336 | 54 | 1169 | 132 | 16.17 | 430 | 343 | 325 | 227 | 331 |
11 | 19:00 | 1399 | 58 | 1166 | 110 | 16.34 | 434 | 323 | 320 | 230 | 327 |
12 | 19:30 | 1526 | 61 | 1166 | 122 | 16.54 | 383 | 334 | 325 | 277 | 333 |
13 | 20:00 | 1471 | 66 | 1145 | 132 | 16.74 | 374 | 326 | 319 | 289 | 317 |
14 | 20:30 | 1599 | 65 | 1123 | 110 | 17.00 | 366 | 300 | 359 | 305 | 336 |
15 | 21:00 | 1496 | 55 | 1104 | 132 | 17.36 | 336 | 233 | 413 | 287 | 370 |
16 | 22:00 | 1282 | 48 | 1105 | 178 | 17.34 | 467 | 378 | 302 | 195 | 365 |
17 | 22:30 | 1085 | 37 | 1086 | 144 | 17.69 | 428 | 441 | 329 | 280 | 370 |
18 | 23:00 | 1049 | 31 | 923 | 90 | 17.64 | 430 | 489 | 313 | 229 | 365 |
19 | 23:30 | 1535 | 88 | 815 | 106 | 17.71 | 335 | 398 | 238 | 259 | 308 |
20 | 24:00 | 1622 | 128 | 819 | 173 | 17.96 | 454 | 348 | 324 | 239 | 341 |
| 平均 | 1706 | 118 | 1096 |
|
| 355 | 331 | 298 | 251 | 309 |
| 合计 |
|
|
| 1971 |
|
|
|
|
|
|
铁。23:59时9#、10#、11#、12#、13#风口边缘挂渣明显,其余风口基本都黑,0:14时铁口出水,0:17时休风,空料线结束。降料面操作完毕,历时11小时30分钟。
高炉降料面过程参数
表.二
2.3. 炉前放残铁工作
为了尽可能出净渣铁,通过对停炉料的理论计算,结合实际出铁情况,从空料线开始就决定出三炉铁,前两炉铁基本按照正常间隔时间出铁,30--40分钟左右打开铁口,最后一炉在料面降到炉腹下沿风口发黑时再出铁。通过对停炉料的理论计算应出铁水541.8t,实际出铁水599.9吨,两者相差58.1吨,从实际扒炉现场观察基本达到目标要求。
残铁重量、成份、及炉渣成分
表.三
炉号 | 出铁时间 |
| 生 铁 成 分 | ||||||
开口 | 堵口 | 过磅产量 | Si | Mn | P | S | C | Ti | |
54016 | 7:22 | 8:10 | 178.56 | 0.68 | 0.23 | 0.102 | 0.023 | 4.97 | 0.064 |
54017 | 13:14 | 13:56 | 91.24 | 1.55 | 0.32 | 0.128 | 0.016 | 4.7 | 0.13 |
54018 | 14:40 | 15:48 | 211.22 | 1.45 | 0.26 | 0.108 | 0.016 | 5.32 | 0.118 |
54019 | 22:28 | 0:17 | 118.92 | 2.64 | 0.28 | 0.129 | 0.025 | 4.77 | 0.168 |
表.四
炉号 | 出铁时间 |
| 炉 渣 成 份 | |||||||||
开口 | 堵口 | 过磅产量 | SiO2 | CaO | S | R2 | FeO | MgO | Al2O3 | MnO | TiO2 | |
54016 | / | / | / | / | / | / | / | / | / | / | / | / |
54017 | 13:14 | 13:56 | 91.24 | 31.48 | 37.03 | 0.91 | 1.18 | 0.32 | 10.61 | 15.69 | 0.13 | 0.38 |
54018 | 14:40 | 15:48 | 211.22 | 30.56 | 37.73 | 0.97 | 1.23 | 0.26 | 11.05 | 16.31 | 0.11 | 0.32 |
54019 | / | / | / | / | / | / | / | / | / | / | / | / |
4、停炉结语
1. 降料面的前期尽量保持较高风压、顶压、风温,能加速降料面的进程。
2. 本次降料面采用自制改进雾化打水枪,全开氮气阀门,增加了炉内氮气量和打水量,提高了打水的雾化效果,大大降低了爆震的发生机率,从实际进程看,没有发生一次大的暴震,达到了预期效果。
3. 风温全用:由于打水枪的雾化效果好、水量大(最大90m3/min),发生爆震机率低,本次降料面风温一直全用,只是在料面到达炉腹下沿有吹空现象时,才将风温撤到900℃,从热量方面加速了焦炭的燃烧速度,加快了降料面的进程。
需改进措施
1. 本次降料面由于炉型、设计等原因,东南和西北方向顶温偏差较大,最大偏差相差200℃(西北199℃、东南500℃),东南方向温度高需增加打水量,西北方向需减少打水量,由于单只水枪没有安装流量表,造成单个方向的打水量较难调节,顶温把控困难,建议每个方向的打水枪都安装流量表。
2. 氮气总管和分管应安装流量表,便于实时掌控氮气量,更好的搭配实时水量,保证雾化效果。
3. 可以尝试料面进入炉腹区域时,再进行停止回收煤气操作。
潍钢1360m3高炉本次降料面操作,严格按照停炉预案进行,以降料面过程安全、快速、环保为宗旨,充分结合实际耗风量、顶温、风温情况、前期参照煤气成份的变化,后期利用吨焦耗风量和雷达探尺判断料面,准确的控制了空料线的整个进程,圆满完成停炉降料面操作。
- [腾讯]
- 关键字:无