利用人工神经网络系统提高转炉终点碳温双命中率
浏览:次|评论:0条 [收藏] [评论]
摘要:本文以神经网络为基础开发出一套转炉冶炼终点控制模型。模型以转炉炼钢基础理论为理论依据,采用误差反向传播网络--BP网络为原形,对其算法进行改进,建立两个三层BP预测神经网络,选用29个输入参数,分别对终点温度和终点碳含量进行预报。通过采集现场操作数据和实际应用,碳温双命中率达到80以上。
1 前言
氧气转炉炼钢是一个多元多相高温反应过程,冶炼过程中炉内发生着极其复杂而又激烈的物理化学反应,影响冶炼终点钢水成分和温度的因素复杂多变,采用传统的看火焰凭经验判断冶炼终点的方法,很难一次拉碳达到终点目标值,即终点成分和温度双命中率低。并且我厂由于炉容小,原料品种多,成分复杂而且经常发生变化,岗位操作工水平不一,使得转炉操作有很大的盲目性,过程控制难度大,喷溅、返干严重,物料消耗加大,终点控制不准确,C-T双命中率低,后吹严重,倒炉次数多,不仅影响生产率,更主要导致钢水质量恶化,使产品质量下降,直接违背了邢钢的质量方针。因此无论从降低炼钢成本,还是从提高钢坯质量和保证生产顺利进行的角度来讲,加强钢水的碳温命中率都是十分有意义的。本文将利用B—P型神经网络原理,建立转炉终点钢水碳温预测模型,来处理影响冶炼终点诸多复杂的非线性因素,从而准确的预报冶炼终点,用计算机控制冶炼过程,优化了转炉静态模型。
2 误差反向传播(B—P)人工神经网络
人工神经网络(Artificial Neural Networks)是指在信息和计算机科学等领域内向生物学习过程而构造的神经网络。它是模拟人脑的功能,由大量简单的神经元广泛互联而成为一种复杂网络系统,是对人脑复杂功能的简化、抽象和模拟。其主要特征是:1)表现出像大脑皮层那样有一个广泛连接的巨型复杂系统;2)计算过程建立在大规模并行结构和并行处理的基础之上。单个的神经元非常简单,但是大量功能简单的神经元可以通过一定的拓扑结构,组织起来构成群体并行式处理的计算结构,具有十分强的学习和记忆功能,从而被应用在各个领域。其中BP型神经网络是当今神经网络模型中应用最广泛的一类。
BP模型即误差后向传播神经网络(BackPropagation,简记为BP),是一种多层前馈网络使用的有教师学习算法,实现了多层网络设想。从结构上讲,BP神经网络分为输入层、中间层(隐层)和输出层,层与层之间采用全权值互联方式,同一层单元之间不存在相互连接,三层BP网络结构示意图如下。
BP模型实现了多层网络学习的设想,它有输入层节点,输出层节点和隐层节点。当给定一个输入模式时,输入信号先向前传播到隐节点,经过隐节点作用函数处理后再输送给输出层节点,最后由输出层节点处理后输出结果。每一层神经元的状态只影响下一层神经元的状态。如果输出响应与期望输出的差值超出了误差范围,不满足要求,就转入误差向后传播,将误差信号沿着原连接通路返回,修改各层神经元的连接权值。对于给定的一组训练样本,不断的用一个个训练样本训练网络,重复前向传播和误差向后传播过程,当每个训练样本都满足要求时,我们就说BP网络训练好了。这就是B—P网络的学习思想。
3 神经网络预报系统
3.1 神经网络模型的建立
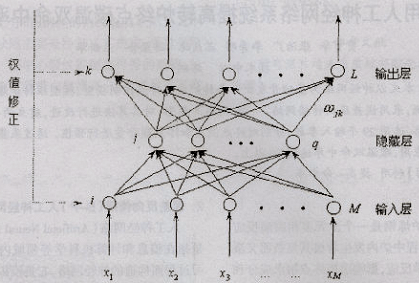
(1)模型的选定
经查阅文献资料,综合比较后,确定采用BP算法来构建神经网络。
(2)网络个数的确定
网络各个输入参数对温度和碳含量的影响程度是不一样的,为了防止互相干扰,建立终点温度预报和终点碳含量预报两个网络模型,并且这两个网络各自独立学习,分别进行预报。
(3)神经网络数据处理
为实现神经网络的联想记忆功能,在网络训练时,首先要求提供给网络一组适当数量的可靠样本。在对大量样本学习的基础上,不断地修改权值和阈值,正确地反映输入变量与输出变量之间的映射关系。选择了300炉的生产数据,并以前200炉数据作为学习样本库,后100炉数据作为预报对照数据。
(4)模型输入参数的确定
为了有效地进行转炉终点温度和终点碳含量预报,合理的选择输入参数是至关重要的。参数选的太少,可能忽略某些影响因素,导致命中率低;相反,如果参数选的太多,会增加网络的复杂程度,网络迭代时间变长,导致无法收敛或收敛时间过长。在进行选择时,必须筛选与转炉终点控制相关度较大、变化较为敏感的参数。本网络选取了29个主要影响因素作为输入参数,如下表所示。
序号 |
输入参数 |
序号 |
输入参数 |
1 |
空炉时间 |
16 |
铁水中P含量 |
2 |
铁水装入量 |
17 |
铁水中S含量 |
3 |
废钢装入量 |
18 |
上炉溅渣时间 |
4 |
铁块加入量 |
19 |
铁块中C含量 |
5 |
氧化铁皮加入量 |
20 |
铁块中Si含量 |
6 |
镁球加入量 |
21 |
铁块中Mn含量 |
7 |
石灰加入量 |
22 |
铁块中P含量 |
8 |
轻烧白云石加入量 |
23 |
铁块中S含量 |
9 |
萤石加入量 |
24 |
钢水中C含量 |
10 |
吹氧量 |
25 |
钢水中Si含量 |
11 |
吹氧时间 |
26 |
钢水中Mn含量 |
12 |
入炉铁水温度 |
27 |
钢水中P含量 |
13 |
铁水中C含量 |
28 |
钢水中S含量 |
14 |
铁水中Si含量 |
29 |
钢水温度 |
15 |
铁水中Mn含量 |
|
|
(5)模型输出参数的确定
本系统以终点温度预报网络和终点碳预报网络两个变量作为输出参数。
(6)网络其他参数设定
网络层数
理论早已证明:具有偏差和至少一个S型隐含层加上一个线性输出层的网络可以逼近任何有理函数。从提高误差精度和训练效果两方面综合考虑三层网络比较合适。故本网络设定为三层网络。
中间层节点数的确定
按经验公式,最终选定中间层节点数为30个。
模型与散状料自动加料系统的连接
神经网络终点预报系统通过excel电子表格与wince自动加料控制系统连接。当预报的终点碳和温度与目标值相符合时,将各种散状料预加入量数值记录下来,并通过代码分批次存储到excel表格内,由wince系统从excel表格内读取数据并控制加料系统自动称量和加料。真正实现了加料过程的计算机自动控制。
4 模型在现场的应用
4.1 具体模型操作如下:
启动“邢钢转炉冶炼专家控制系统”后,点击“神经网络”按钮可进入“欢迎使用神经网络辅助控制系统”界面。窗体中有两个按钮“进入”按钮和“退出”按钮。点击“进入”按钮将进人“神经网络预测系统”,点击“退出”按钮将退回到“邢钢转炉冶炼专家控制系统”界面。
欢迎使用“神经网络辅助控制系统”界面如下图所示:
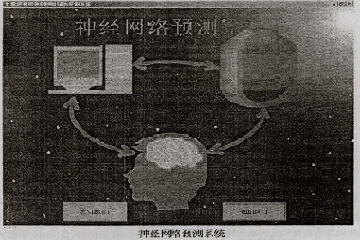
进入“神经网络预测系统”后如下图所示:

在各文本框中输入相应的数值后点击“预测”按钮就可以在“预测温度”和“预测含炭量”中显示出预测数值。
在此窗体右侧最下方有“生成样本”按钮,此按钮的作用是:当用户第一次使用此系统时,需要首先建立学习样本。建立方法就是在此窗口各个文本框中输入相应的值,然后点击此按钮则第一组数自动生成样本,然后反复输入其它炉的数据点击此按钮样本就会自动生成了,输入样本的数据为100炉为宜。建完样本后先进行网络学习,然后再依次进行“预测”、“对比曲线”等操。注:此按钮只用于第一次用本程序。
点击“对比曲线”按钮将进入如下窗体:

此窗体主要显示最近冶炼的10炉钢的目标出钢温度和预报终点钢水温度的变化趋势,点击“温度曲线”按钮可进入温度对比曲线画面,通过对两条曲线的对比可以直观看出预测的准确度,并且通过曲线的变化趋势可提示现场操作工人转炉冶炼的总体走向,看是否有必要调节一下原料配比。同理,点击“C含量曲线”按钮可进入碳对比曲线画面。
点击“网络学习”按钮可进入如下窗体:

此窗体的主要功能对是对神经网络进训练,在预测按钮中我们集成了一项数据记录功能,即每炉预测完成的同时它的原料条件也随之保存到了一个数据文件里,这个数据文件实时更新,当冶炼进行到一定程度(如冶炼了几百炉后)或预测精度不够高时我们都可以调出这个画面对网络进行训练,进入这个画面后我们首先在“训练次数”后面的文本框中输入训练次数(我们这里设的最大训练次数为5000次),然后点击“温度网路训练”按钮或“碳含量网路网络训练”按钮就可以对他们进行训练了。后面的文本框中列出了训练的全局误差值,当此值小于0.001时我们认为满足要求可结束本次训练,当误差值大于0.001我们可加大训练次数继续训练。
4.2 现场跟踪数据:
神经网络系统中C-T双命中率进行了数据跟踪试验,具体试验数据如下:
炉号 |
实测 |
神经网络预测 |
备注 | ||
温度 |
碳含量 |
温度 |
碳含量 | ||
20400309 |
1653 |
0.07 |
1657 |
0.072 |
C-T双命中 |
20400310 |
1654 |
0.07 |
1658 |
0.074 |
C-T双命中 |
20400317 |
1649 |
0.09 |
1652 |
0.085 |
C-T双命中 |
20400318 |
1641 |
0.07 |
1657 |
0.083 |
C-T未双命中 |
20400319 |
1662 |
0.08 |
1658 |
0.075 |
C-T双命中 |
20400321 |
1671 |
0.07 |
1668 |
0.075 |
C-T双命中 |
20400357 |
1680 |
0.06 |
1670 |
0.078 |
C-T未双命中 |
20400358 |
1680 |
0.08 |
1677 |
0.076 |
C-T双命中 |
20400359 |
1680 |
0.08 |
1676 |
0.065 |
C-T双命中 |
20400360 |
1681 |
0.07 |
1678 |
0.065 |
C-T双命中 |
20400361 |
1670 |
0.08 |
1679 |
0.065 |
C-T未双命中 |
20400362 |
1672 |
0.08 |
1661 |
0.07 |
C-T未双命中 |
20400363 |
1668 |
0.09 |
1665 |
0.083 |
C-T双命中 |
20400364 |
1665 |
0.08 |
1665 |
0.084 |
C-T双命中 |
20400365 |
1678 |
0.07 |
1675 |
0.065 |
C-T双命中 |
20400366 |
1677 |
0.07 |
1675 |
0.063 |
C-T双命中 |
20400367 |
1662 |
0.09 |
1665 |
0.085 |
C-T双命中 |
20400368 |
1668 |
0.08 |
1665 |
0.083 |
C-T双命中 |
20400369 |
1663 |
0.09 |
1663 |
0.088 |
C-T双命中 |
20400370 |
1673 |
0.05 |
1665 |
0.085 |
C-T未双命中 |
20400371 |
1665 |
0.07 |
1663 |
0.072 |
C-T双命中 |
20400372 |
1658 |
0.08 |
1664 |
0.075 |
C-T双命中 |
20400373 |
1660 |
0.08 |
1662 |
0.081 |
C-T双命中 |
20400374 |
1667 |
0.07 |
1665 |
0.075 |
C-T双命中 |
20400375 |
1666 |
0.073 |
1663 |
0.076 |
C-T双命中 |
20400376 |
1655 |
0.09 |
1661 |
0.071 |
C-T未双命中 |
20400378 |
1653 |
0.09 |
1658 |
0.085 |
C-T双命中 |
20400379 |
1672 |
0.06 |
1668 |
0.056 |
C-T双命中 |
20400380 |
1675 |
0.06 |
1670 |
0.062 |
C-T双命中 |
20400381 |
1670 |
0.07 |
1672 |
0.065 |
C-T双命中 |
20400382 |
1665 |
0.075 |
1668 |
0.072 |
C-T双命中 |
20400383 |
1672 |
0.06 |
1668 |
0.06 |
C-T双命中 |
20400384 |
1670 |
0.06 |
1668 |
0.061 |
C-T双命中 |
20400385 |
1663 |
0.06 |
1663 |
0.06 |
C-T双命中 |
20400386 |
1665 |
0.07 |
1669 |
0.075 |
C-T双命中 |
20400387 |
1670 |
0.07 |
1670 |
0.071 |
C-T双命中 |
20400388 |
1658 |
0.08 |
1663 |
0.073 |
C-T双命中 |
20400 |
1662 |
0.07 |
1662 |
0.071 |
C-T双命中 |
通过以上三十八炉数据,可以看出碳温双命中率达到84.2%。
4.3 效益分析
利用神经网络软件提高转炉终点碳温双命中率,提高一次拉碳率,比原来缩短冶炼周期0.8分钟,增产62856吨钢坯,每吨钢坯盈利497元考虑,年创(增)效益628563497=3124万元。
5 结论
(1)人工神经网络技术建立转炉冶炼终点静态控制模型,解决了常规静态模型很难处理的许多复杂的非线性关系等难题,在转炉炼钢控制方面具有广阔的发展前景。
(2)以BP网络为基础的转炉终点预报模型,并建立了可保存100炉数据的学习样本,用来对网络进行实时训练,使模型适应生产条件的变化。当设定温度误差为±5℃,碳含量误差范围为±0.01%时,终点温度命中率为89%,终点碳命中率为75%。该神经网络模型具有较高的预报精度
(3)可以利用本模型得到的结果对生产工艺参数进行调整,以达到预期的目的。
- [腾讯]
- 关键字:无